This is a flexible and efficient method for producing high-quality metal parts and components. This guide contains all the necessary information to enable you walk through the process of spin casting metal; it highlights important equipment, materials and techniques in order to achieve better results. It will provide insights into the use of spin casting machines as well as a range of alloys that are appropriate for this process, for both beginners who would like to learn the basics of spin casting as well as those who have been practicing this artform for a long time now. Join us in exploring the fascinating world of spin casting while discovering how intricate metallic objects can be crafted with precision and ease.
What is Spin Casting and How Does it Work?
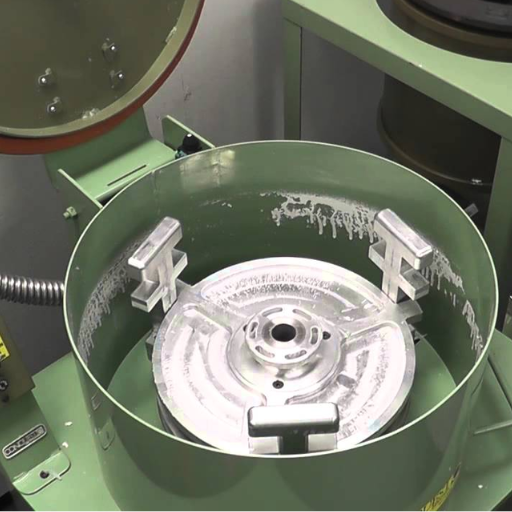
Image source: https://www.youtube.com/
Spin casting also known as centrifugal rubber mold casting is an industrial process whereby molten metal is poured into a spinning mold. At first, silicon or rubber mold is prepared which is placed inside a spin caster machine. When at high speed, the spinning force pushes melted metal into molds’ fine crevices ensuring equalty and reduced chances of air entrapments during solidifications. This method is suitable for small complex parts due to their excellent surface finish and tight tolerances. The most common metals used in centrifugal molds are pewter among others like zinc since these have low melting points. Rapid spinning combined with versatile molds allows manufacturing at shorter times making it cost effective production of superior quality metallic parts.
Understanding the Spin Casting Process
The spin casting method starts with the design and fabrication of a very accurate mold, usually made from rubber or silicone. This means that the shape as well as other fine details on the cast can be dictated by this particular mould. Finally, the mold is placed in position inside a spin casting machine that holds it firmly. The machine applies centrifugal force created through high-speed rotation to make certain all parts of the molten metal flow into every narrow space within the cavity.
Afterwards, this filling process involves pouring molten metals which include alloys such as zinc, pewter and other low-temperature melting metals into the previously prepared molds. While spinning, gravity pulls outwards forcing molten metal to go across all areas of the mold uniformly. The fast spinning helps reduce air bubbles and imperfections which in turn give rise to components possessing high dimensional accuracy coupled with excellent surface finish. When cooled down and solidified, metal is released from its casing or outer shell exposing complete final parts for further treatment such as polishing or coating. Spin casting is esteemed because it permits rapid formation of intricate objects at reasonable costs hence popular with manufacturers.
Key Components of a Spin Casting Machine
A spin casting machine usually consists of some vital parts that work in harmony to generate high-quality castings.
- Mold Chamber: This is the cavity where the mold is securely positioned when casting operations are done. It has been made in a way that it can withstand higher rotational forces and ensure that the mold does not move during operation.
- Rotating Plate: The central point of this machine, this rotating plate or turntable bears the mold chamber, which spins at very high speeds. The centrifugal force produced by its rotation is important for distributing molten metal throughout the mold’s cavities evenly.
- Heating System: Many spin casting machines have heating systems for maintaining and controlling molten metal temperature. Casting quality remains consistent due to optimal temperatures maintained by the heating system.
- Injection Mechanism: This component deals with injecting molten metal into a mold. The injection mechanism ensures precise control enabling accurate molding of objects through delivering right quantities of metals.
- Control Panel: Such panels allow operators to adjust different parameters of castings including rotation speed, temperature, timing etc. Some advanced control panels come with digital displays and may have programmable settings for increased accuracy as well as repeatability.
- Cooling System: Proper cooling should be applied after casting process when removing molded part from die. A cooling system assists in speeding up solidification processes so that there is less time wasted on having completed products removed and readied for next cast cycle.
By interconnecting these principal parts, spin casting machines can produce intricate designs and shapes while reducing defects hence making them cost effective manufacturing methods at low costs.
Materials Used in Spin Casting
Typically, spin casting employs a wide range of materials that may be chosen for the intended properties of the final product. The commonly used include:
- Alloys: Zinc and pewter alloys are very common because they have low melting points and are easy to work with. These metals display high strength and fidelity of detail which renders them suitable for intricate designs.
- Plastics and Resins: Thermoplastics, as well as polyurethane resins, are also used apart from metals. These can produce parts that are durable and light in weight, while allowing for choice in terms of color and texture.
- Rubber and Silicone: Rubber and silicone materials are widely used in mold-making due to their flexibility and durability. They can withstand temperatures as high as those of molten metal thus providing accurate reusable molds.
How to Choose the Right Metal for Spin Casting
To choose the right metal for spin casting, various factors must be considered including; specific production requirements, final part details’ melting point of the metal among other things.Firstly consider mechanical properties needed like tensile strength, hardness ductility et cetera. For instance, zinc alloys make excellent high-strength parts with intricate details while pewter alloys make better fine decorative objects due to their smooth finish and lower melting point. Also check if the metal melts at a temperature within your machine’s capability. Melting-point metals such as zinc or pewter mean less demanding work on molds. Lastly think about how much it will cost you to buy the material plus if it is available locally or not? Common ones like zinc will often be cheaper than others hence better for large scale productions When all these considerations have been carefully taken into account choosing a metal then should allow you to meet production needs while ensuring quality at reasonable prices.
Popular Alloys for Spin Casting
- Zinc Alloys: These materials are some of the most commonly used in spin casting and are known for their high strength, good dimensional stability and ability to produce detailed features. Zinc alloys are flexible and able to provide a good balance between cost, ease of casting, and strength. In particular, they can be used to make parts that must last long enough.
- Pewter Alloys: Pewter is an alloy made predominantly from tin along with antimony or copper which is popular in the production of decorative articles and fine details. With it having low melting point it becomes easy to cast pewter as well as extending the life span of molds used in casting. Using pewter alloys results in smooth finishes thus making them appropriate for artistry as well as ornamental objects.
- Lead-Tin Alloys: These types of alloys have been chosen due to their low melting points and ease of castability. This means lead-tin alloys can be easily fashioned into highly finished products with intricate features like model figures or small decorative items produced in limited quantities. However, because lead is toxic, care must be taken when handling and pouring such substances.
Properties of Zinc Alloy and Pewter
Besides, zinc alloy and pewter have unique characteristics that make them suitable for spin casting.
Zinc Alloy Properties:
- Strength and Durability: Strong tensile strength and durability that are associated with zinc alloys makes them ideal for making robust parts.
- Dimensional Stability: This is because they offer excellent dimensional stability, thus ensuring consistency and accuracy in the components made from it.
- Corrosion Resistance: In addition, this material can withstand corrosion to a good extent, thereby prolonging its lifespan.
- Ease of Casting: The average melting point of zinc alloy is such that it flows easily into molds taking up very detailed features hence, facilitating production efficiency cycles.
Pewter Properties:
- Low Melting Point: Due to its low melting point, the energy costs required to melt pewter decrease while the life span of the casting mold increases accordingly.
- Smooth Finish: Pewter castings produce a smooth surface finish with high quality results; hence it is desirable for decorative arts.
- Malleability: This means that pewter is malleable enough such that fine details would be invisible if made using any other methods; especially when one wants to make delicate patterns.
- Aesthetic Appeal: It has an attractive metallic sheen resembling silver-gray often used on ornaments because of its visual appeal.
These properties enable producers to select the right materials depending on the specified needs of their products.
Advantages of White Metal in Spin Casting
The term white metal is a general name for different types of alloys based on lead and tin, which have a wide range of applications in spin casting.
These metals are highly flexible; they can accommodate simple as well as complicated designs with precision.
This type of metal is cost effective. The fact that it requires less energy to cast these metals because their melting point is lower makes them more affordable in terms of raw materials costs.
White metals can effectively capture minute details, hence are suitable for intricate and accurate purposes.
These metals are easy to handle due to low melting points and require less energy which saves costs at large scale or huge production volumes.
They possess good mechanical properties that ensure the strength and durability of various products made from such metals thereby guaranteeing the life reliability.
White metals cool and solidify faster leading to shorter cycles times during production thus fast turnover rates are possible with high quality castings being produced as a result.
Advantages like these make white metals attractive options for manufacturers seeking to balance expenditures, output timeframes, and the quality associated with their spin casting procedures.
What Equipment Do You Need for Metal Casting?
To perform metal casting, there are a number of crucial equipment that must be in place:
- Melt Furnace: Necessary as it will be used to change the state of the metal into liquid.
- Molds: These are shaped containers which melted metals are poured into.
- Crucibles: They hold molten metals when they have already liquefied in furnaces.
- Ladles: These tools facilitate movement and pouring of molten metal into molds.
- Tongs: These are used to safely handle hot crucibles and moulds.
- Protective Gear: Including gloves, aprons, and face shields to protect against the intense heat and potential splashes of molten metal.
- Ventilation Systems: They must be present as they are necessary for expelling poisonous gasses formed during the process of casting
- Cooling Systems: This ensures that the solid metal turns out all right in quality when turning from liquid stage.
Therefore, with this particular model, the procedure of casting is efficient saving time and good results can be expected.
Essential Casting Equipment
First, when performing metal casting, there are a number of equipments that should be put into consideration:
- Melt Furnace: With the use of this instrument it is possible to heat or melt the solid metal so that it changes from its solid state to liquid state. The furnace chosen is dependent on the type and quantity of metal.
- Molds: This form of casting provides the framework for the molten metals in order to give them their desired shape. They can be created from such materials as sand, metallic or ceramic flaked bodies which depends upon the method of casting among other factors.
- Crucibles: Crucibles are resistant containers that hold melted metals in a furnace. Such crucibles ought also to bear high temperatures and resist corrosion by these solutions.
These main equipment would not be complete if not accompanied by some tools such as ladles through which hot metal can be poured; tongs for safety purposes; protective clothing for worker’s safety; ventilation systems to suck harmful fumes while cooling systems regulate solidification process on aflawless way, resulting better quality castings. Choosing and maintaining these equipments is key to efficient, safe and high-quality casting outcomes.
Types of Spin Casting Machines
Spin casting machines are central in many industries due to their efficient production of detailed and quality metallic casts. The key kinds of spin casting machines include:
- Centrifugal Casting Machines: These machines operate by rotating molds at high speeds, forcing the molten metal to the mold’s outer edges using centrifugal force. This kind of machine is especially good at making tubular products like pipes and bearing races.
- Vacuum Spin Casting Machines: These machines make use of a vacuum system during casting so as to get rid of air entrapment or porosity in its final product. Vacuum spin casting is suitable for delicate parts and high precision jobs, often seen in the jewelry as well as aerospace industries.
- Horizontal Spin Casting Machines: During the stage where the rotation is taking place, these machines situate moulds horizontally for equal spread of liquid metal. They are generally applied in the manufacture of large, intricate castings and can accommodate various metals/alloys thus increasing production flexibility.
For every species of spin casting machine, there is a specific aspect that it has been designed to optimize during the casting process thereby enabling them to produce high quality results which meet different application requirements. The choice made based on what one wants will enable them determine if their selection will result into optimal performance or not.
Importance of a Quality Melting Furnace
There are a few reasons why a spin casting process requires an efficient melting furnace. The most important of these is that it makes sure that the metals are uniformly heated and melted, thereby ensuring uniform and high quality castings. This means that good quality furnaces can prevent any oxidation or other forms of contamination in the metal casting. In addition, modern furnaces consume less energy and as such they contribute to lower operational costs and have low environmental impacts. Moreover, where there is a reliable and longer lasting burning unit, this ensures that it is going on at all times minimizing any instances of failures in the operation’s productivity hence reducing down time as well as maintenance costs. Consequently, choosing the best melting furnace can be seen as one way through which an ideal spin casting process can be optimized in terms of cost effectiveness in relation to its efficiency as well as quality.
How to Create Molds for Spin Casting?
Creating molds for spin casting involves many essential steps, which must be given close attention to achieve accurate and excellent results:
- Design the Mold: The initial stage is designing a mold based on the product intended for the final outcome. CAD software usually comes in handy when developing detailed and precise designs that can accommodate complex geometries.
- Select Mold Material: Usually one goes for good heat resistive material like silicone or vulcanized rubber due to their resiliency and ability to produce a mold with fine details.
- Create a Master Pattern: Come up with a master pattern of the object you want to cast. This can be made of various materials including wax, clay or 3D printed plastics among others. A master pattern should match exactly what will be produced finally.
- Build the Mold Frame: Design a frame which will hold the molding material referred as a mold box. It should be strong enough so as not to collapse when subjected to casting forces.
- Position the Master Pattern: Put master pattern within the mold frame ensuring that it is well positioned and allowing enough space around it where mold material can fill creating an appropriate cavity.
- Pour the Mold Material: Make use of careful pouring techniques while filling up your selected mold material slowly inside the frame so that it covers completely all over your master pattern removing any air bubbles that may affect accuracy of your mold.
- Cure the Mold: Leave the vulcanizing rubber in accordance with manufacturer’s instructions until it cures by heat application so that it hardens and preserves its make-up at last.
- Remove the Master Pattern: Once set properly, take off both the mould from mould frame then pull out master pattern hence leaving behind hollow where every design detail has been captured in it.
By these steps you will have molds ready for use in spin casting process leading to high quality casts which are full of details.
Silicone Rubber Molds
Their versatility, durability, and ability to capture intricate details make silicone rubber molds very popular in the casting industry. Furthermore, they are particularly useful in producing multiple castings with uniform quality. Here is a brief summary:
- Versatility: Silicone moldings can be used with various casting materials like resins, wax and some low-metal alloys.
- Durability: In comparison to other molding materials, silicone has excellent tear strength and it can be used repeatedly without serious failures.
- Detail Capture: Defining features of silicone molds include its ability to capture fine detail due to flexibility. Also this reduces the onset of air bubbles as a result of its relatively low viscosity.
- Ease of Use: Creating silicone molds is easy and does not require special equipment; hence it is suitable for beginners as well as experts.
- Temperature Resistance: This material can withstand a wide temperature range which is important for some casting processes involving heat.
These attributes have made silicone rubber molds one of the best choices when making high-quality and dependable molds during casting.
Vulcanizing Process for Mold Preparation
The vulcanization process is crucial when making molds for casting, particularly using rubber or silicone materials. Here is a brief overview based on the top content from reputable websites:
- Material Selection: Choose an appropriate rubber mixture which corresponds to the requirements of the casting material.
- Mold Assembly: The master pattern has to be arranged in such a way that it fits well within the frame of the mold and properly placed.
- Heating: A controlled heating source, usually either heated press or oven, subjects the mould that contains a pattern therein.
- Pressure Application: During heating, apply pressures which are even so as to cause uniform flow of rubber around patterns by eliminating air bubbles and capturing fine details.
- Curing: As heating takes place, rubber undergoes curing (vulcanization) through this chemical reaction whereby rubber gets stronger hence more capable of withstanding repetitive use.
- Cooling and Demolding: Cooling should be conducted slowly after heating and curing in order to prevent any warping; when cooled down completely, then open up molds and check if master patterns should be taken out thereby leaving behind sturdy accurate cavities for casting purposes.
By following these steps one can achieve high-quality, long-lasting molds fit for different types of casts.
Differences Between Rubber Mold and Silicone Mold
You must be able to distinguish between silicone molds from rubber molds if you are going to choose a good material for your casting needs. Here is a brief comparison that should help you:
- Material Composition:
- Rubber Molds: Usually, these molds are made out of natural or synthetic rubbers such as polyurethane or latex and they are known for their flexibility and durability.
- Silicone Molds: On the other hand, silicone rubber is used to make these molds which can tolerate extreme temperatures and have higher tear strength.
- Flexibility and Durability:
- Rubber Molds: They allow some bending without tearing, but this material may break down over time when exposed to UV light or certain chemicals, including petroleum products.
- Silicone Molds: More flexible; therefore, endure longer use because they do not degrade with wear like their counterparts.
- Temperature Resistance:
- Rubber Molds: Useful for materials with low melting point but deform at high heat.
- Silicone Molds: Can handle wide temperature ranges so they are suitable when working on matters requiring curing or involving intense heat levels.
- Chemical Resistance:
- Rubber Molds: In general terms, it has lesser resistance towards chemicals, oils and solvents meaning that the lifespan of the mold could be shortened by these elements.
- Silicone Molds: It is resistant against chemical attack and oil penetration thus resulting in long-lasting molds even under severe conditions.
- Detail Capture:
- Rubber Molds: Fine details can be obtained though its accuracy may not be as perfect as that of silicon in reproducing complicated designs.
- Silicone Molds: Has superb detail capture ability hence enabling replication of intricate patterns exactly as they were designed initially.
Whether you pick silicone or rubber depends on what your project dictates in terms of temperature, complexity of the details and exposure to chemicals.
What are Common Problems in Spin Casting and How to Solve Them?
- Incomplete Fill:
- Problem: Mold cavities are not completely filled, hence causing incomplete castings.
- Solution: Increase spin speeds or pour rates to ensure that there is enough centrifugal force to totally fill the cavities. When you do this also ensure that the mold has some vents in it so as to let air escape.
- Air Bubbles:
- Problem: The presence of air bubbles within the cast material leading to defects
- Solution: Proper venting of mould and using vacuum degasser to remove air from casting material before pouring.
- Mold Wear and Tear:
- Problem: Mold degradation after repeated use, affecting the quality of casting.
- Solution: Regularly check for wear on molds replacing them when necessary. Use long lasting mold materials like silicone.
- Misalignment:
- Problem: Moulds that are misaligned leading to off-centered or deformed castings.
- Solution: Align carefully the two halves of molds and tightly fasten them together during casting so as they can remain on their right positions during casting process.
- Material Shrinkage:
- Problem: Cast materials shrinking during cooling, resulting in dimensional inaccuracies.
- Solution: Take into account shrinkage rates in mold design and consider post-cast treatments for mitigating shrinkage effects such as heat treatment for reducing residual stress on cast materials.
- Surface Imperfections:
- Problem: Surface defects like roughness or pitting.
- Solution: Keep the mold surface clean and smooth. To minimize imperfections, use appropriate release agents, control casting materials’ temperature, and cure profile.
By following these simple steps, you will be able to enhance your spin casting projects quality and reduce variation.
Dealing with Flashing of Molten Metal
Flashing depicts any excessive material that gushes out from the mould halves in casting and forms undesired edges or thin sheets on the final product. To address flashing effectively:
- Mold Alignment:
- Ensure Proper Fit: Ensure that both sides of the mould are well fitted. Misalignment may lead to gaps that molten metal may leak through.
- Secure Clamping: Give an enough pressure when clamping the mold to avoid any gaps.
- Mold Condition:
- Regular Maintenance: Keep a regular watch for molds which may cause uneven surfaces and gaps due to wear and tear.
- Use Quality Materials: Instead, prefer high quality materials which are strong so as to reduce wearing with time.
- Control Pouring Process:
- Regulate Pouring Speed: Do not pour too quickly; this action will result in hot metal being forced into spaces where it was not intended for.
- Manage Temperature: Maintain an optimum temperature of the molten metal to ensure its smooth flow without overly much pressure.
By concentrating on these aspects, you can reduce flashing significantly while enhancing your overall cast quality.
Ensuring Proper Solidification
To make sure that the molten metal solidifies properly in spin casting, these factors are considered:
- Cooling Rate: The rate at which the molten material cools down and solidifies can greatly affect the quality of the final product. A gradual cooling process helps to prevent errors like incomplete mold filling or shrinkage. It is also important for reducing internal stresses within the cast, that solidification be even.
- Temperature Control: Proper maintenance of hotness in molten metal before pouring it is necessary. There are two extreme temperatures that should be avoided during this process; very high temperatures cause excessive shrinkage and creation of voids within the casting while very low ones result to premature solidification which means partial fillings of molds. In order to achieve this objective it is necessary to employ temperature controls that are capable of monitoring and adjusting temperatures as required.
- Uniform Mold Temperature: Heating up a mold to even temperature might help in ensuring equal solidification throughout. By so doing, one can minimize thermal gradients across a mold thereby avoiding differential cooled rates responsible for warping or residual stresses on a casting.
- Alloy Composition: Solidification is also influenced by composition of metal alloys used in spin casting. Different alloys have different characteristics like melting point and cooling behavior. Therefore, appropriateness of alloy selection by matching with specific requirements regarding your project could enhance better solidification and general casting quality.
You can use these principles to optimize solidification thereby improving structural integrity and quality on your cast products.
Maintaining the Spin Casting Machine
To make the spin casting machine work well and serve for a long time, it is necessary to take care of its proper maintenance. Regular cleansing helps to prevent any build-up of deposits that may affect the quality of castings. Inspection and greasing of moving parts like spindle and bearings reduces wear thereby minimizing the chances of breakdowns. The calibrations should as well be done on timely basis in order to maintain correct speeds and temperature settings while rotating molds in the machine. Additionally, immediate replacement of faulty components will keep it running at an optimum level hence preventing costly production down times. By sticking to a consistent timetable for maintenance, you can be sure that your spin casting machine will run smoothly giving high-quality molded items.
What Advanced Techniques Are Used in Spin Casting?
Vacuum Casting
During vacuum casting process, the mold is entirely emptied of air through a vacuum. Such an action is important for reducing air bubbles and refining precision and surface finishing of cast products.
Preheating the Mold
The preheating of molds can help to reduce thermal shock and control solidification more effectively. This eliminates defects and improves the integrity of final castings.
Use of Die Coatings
Specialized die coatings help make it easy to remove the final casting by improving its mold release properties. On the other hand, they boost life span of molds while enhancing the cast part’s surface finish.
Real-Time Monitoring
To sustain optimum casting conditions, actual time monitoring systems which trace temperature, rotation speed as well as other critical parameters can be employed. This ensures that any instances that may negatively affect quality are identified in good time.
These advanced techniques have shown potential for greatly boosting efficiency, quality, and accuracy in spin casting processes.
Centifugal Rubber Mold Casting
Rubber centrifugal mold casting involves pouring molten material into a hollow cavity created inside a rubber tube using centrifugal force. This particular technique has been recognized for its ability to create intricate designs with high-quality finishes on them. By spinning the mold along either a horizontal or vertical axis, molten material gets pushed towards the walls resulting in an even distribution and minimal air entrapment within it.
This technique finds wide application in making small fine-detail components such as jewelry, dental restorations and prototype parts. Rubber molds are preferred because they can take details from original models easily since they are flexible and can resist wear for long periods. Therefore removal of these cast parts becomes less difficult hence increasing their chances of not being damaged when tampered with by other people or factors like weather conditions or environment temperatures where they are used most times outside homes with straight up sides covered for protection; further there is also reduction in manufacturing cost due to repetitive use without changing the mold producing many copies of a single piece which is in turn cost effective.
Rapid Prototyping
Rapid prototyping is an inventive process which allows a fast creation of a physical model, part or assembly using 3D computer-aided design (CAD) data. Product development would highly benefit from this technique as it helps designers and engineers create functional prototypes and test their designs before embarking on full-scale production. The most common methods for rapid prototyping include 3D printing, stereolithography (SLA), and selective laser sintering (SLS). These methods have dramatically changed the manufacturing industry through reducing time and cost associated with traditional prototyping processes. Rapid prototyping enables early recognition and adjustment of design failures in order to enhance efficiency in developing products.
Using Modern Spincasting Machinery
Modern spincasting machines are doing much to elevate precision engineering by improving efficiency and consistency in producing high detailed casted components. They are built with features such as automated temperature control, programmable spin speeds, and augmented safety programs that make casting environment favorable for casting leading to excellent finished product quality. The precision of these parameters allows them to have better control over the process thus resulting into high quality finished products that are uniform in their nature. Besides, current spincasting machinery often integrates vacuum systems in order to eliminate air pockets thereby enhancing the accuracy and detailing of casts items. Spincasting has been made more reliable and cost efficient through automation therefore enabling the production of complex intricate designs on a large scale.
Frequently Asked Questions (FAQs)
Q: What is spin casting and how does it differ from other casting techniques such as sand casting and die casting?
A: Spin casting, also known as centrifugal rubber mold casting, uses centrifugal force to ensure the molten metal or casting material is distributed evenly within the mold. Unlike sand casting which uses sand molds and die casting that forces molten metal into die molds under pressure, spin casting often utilizes vulcanized silicone or rubber molds for better detail and efficiency.
Q: What are the essential components of spin casting equipment?
A: Essential components of spin casting equipment include the spin caster, metal molds, a vulcanizer for mold preparation, a platen to hold the molds, and a source for molten metal such as a metal alloy. Replacement parts like sprues and blades (knife or scalpel) for cutting molds are also important.
Q: How does a vulcanizer function in spin casting?
A: A vulcanizer is used to create durable and heat-resistant molds by a process called vulcanization. This involves heating rubber or silicone with sulfur or other curatives, resulting in vulcanized molds that are ideal for repeated casting cycles in a spin caster.
Q: When should I replace parts like the sprue in a casting mold?
A: Replacement parts like the sprue should be replaced when they show signs of wear or damage that could impact the quality of the cast. Frequent checks and maintenance ensure consistent surface finish and reduce casting defects.
Q: What metal alloys are commonly used in spin casting?
A: Common metal alloys used in spin casting include zamak, white metal alloys, pewter, and other low melting point alloys. These materials offer good flow properties and solidify quickly, making them ideal for centrifugal casting processes.
Q: How does the centrifugal force in a front-loading spin caster impact the casting process?
A: The centrifugal force generated by a front-loading spin caster forces the molten metal into every cavity of the mold, ensuring thorough and even filling. This results in detailed and precise castings with minimal defects.
Q: What is the difference between a top-loading and front-loading spin caster?
A: The main difference lies in how the mold is positioned and accessed. A top-loading spin caster has the mold placed vertically from the top, while a front-loading spin caster allows horizontal placement and access from the front. Front-loading systems often provide better control and ease of use.
Q: How does metal cooling impact the final product in the spin casting process?
A: Proper metal cooling is crucial in the spin casting process. Rapid and even cooling results in a better surface finish and reduced internal stresses in the casting material. Inconsistent cooling can cause warping, shrinkage, and other defects.
Q: Can spin casting be used for large-scale commercial production?
A: Yes, commercial spin casting is widely used, especially for creating small to medium-sized parts. It offers cost advantages and faster production cycles compared to techniques like investment casting or die casting and injection molding.