In creating and making things 3D printing technology has made a revolution, availing countless possibilities for innovation and customization. The 3D printing process involves several important steps. One of them is to choose the right filament material to use which can be very confusing as there are many. Among the common choices of filament materials include ABS (Acrylonitrile Butadiene Styrene) and PLA (Polylactic Acid). This blog post will give you in-depth knowledge on PLA vs. ABS: comparison of their properties, advantages and potential applications thereof in order to enable you make an informed decision.
What Are the Key Differences Between PLA and ABS Filaments?
Image source: https://medium.com/
PLA differs from ABS filaments based on factors such as composition, ease of application, and mechanical properties among others. Unlike ABS that is petroleum-based thermoplastic with higher melting point and durable at the same time, PLA is a biodegradable thermoplastic that comes from renewable resources like corn starch or sugar cane thus considered more eco-friendly than other types. It prints easier because it requires lower temperature during printing besides having fewer deformations. However, it should be noted that this plastic type emits highly harmful fumes after heating up. Well ventilated enclosed workspace is advised when using this material so that these fumes don’t have any effect on people’s health if they breathe them in unknowingly. So, you need to consider environmental impact, ease of usage and mechanical requirements in the application when choosing between PLA or ABS for your project needs.
Physical Properties of PLA and ABS
PLA
- Melting Point: In general, PLA has a melting temperature range of 180°C to 220°C, which makes it easier for hobbyist 3D printers to access.
- Density: PLA is slightly more dense than ABS and usually has a density of about 1.24 g/cm³.
- Strength and Rigidity: PLA is known for its rigidity and strength (which are enough for aesthetic and low-stress applications) but also its brittleness when compared to ABS.
- Biodegradability: PLA stands out due to its ability to decay through industrial composting conditions.
- Surface Finish: Prints created with PLA exhibits smooth finish especially at lower layer heights.
ABS
- Melting Point: On the other hand, ABS melts at higher temperatures ranging from 210°C-250°C making it difficult to print without a heated bed.
- Density: The material is less dense with an approximate density of around 1.04 g/cm³.
- Durability and Flexibility: For instance, ABS has high durability hence can endure more stress or strain without breaking thus making it suitable for mechanical parts and high impact applications such as machinery parts.
- Heat Resistance: Additionally, ABS can tolerate greater degrees of hotness without warping hence suitable for pieces exposed to heat.
- Surface Finish: Further smoothing can be done on prints made using ABS by means like acetone vapor treatment that improves layer adhesion as well as surface quality too.
Understanding these physical properties will enable you to choose the right filament for your specific needs in 3D printing.
Chemical Resistance of PLA and ABS
PLA: Polylactic Acid (PLA) demonstrates a medium chemical resistance, but it is vulnerable to degradation in environments which contain solvents such as acetone, ethyl acetate and MEK (methyl ethyl ketone). It is resistant to oils and greases; however, it might get damaged when exposed to highly alkaline or acidic conditions. Consequently, PLA is not the best choice for applications involving extreme chemical exposure or prolonged immersion.
ABS: Acrylonitrile Butadiene Styrene (ABS) boasts of extensive chemical resistance when compared with PLA. It works well in presence of numerous acids & alkalis, alcohols and oils. But it is impaired by solvents like acetone that can dissolve ABS which makes it more useful for post-processing but less tolerable in solvent-exposed locations. Therefore, ABS’s strong chemical resistance makes it ideal for industrial applications where a variety of chemicals are used.
It is important to appreciate the chemical-resistance values of these materials when choosing the right filament for any application that may handle different types of chemicals or solvents.
Print Temperatures for PLA and ABS
One may print PLA with 3D, recommended print temperature is between 180°C and 220°C. This temperature is quite low hence ideal for most of the standard 3D printers and also guarantees consistent extrusion as well as good layer adhesion across every part that gets added. For a better outcome, it may be necessary to adjust the particular temperature within this range depending on the brand of PLA or the printer’s environment.
However, ABS needs high print temperatures ranging from 220°C to 250°C. In this regard, these higher temperatures are required to properly melt and extrude ABS which has a melting point that is higher than that of PLA. Additionally, often times when printing with ABS, a heated bed set ranging between 90°C and 110°C is used so as to reduce warping and enhance bonding between layers.
Therefore, choosing appropriate print temperatures for PLA and ABS would lead to quality prints while common issues like warping or poor adhesion can be reduced. Similarly, slight adjustments of such temperatures can still boost print quality in consideration of your exact printer set up as well filament type used.
Advantages of Printing With PLA Compared to ABS
Printing with PLA has a lot of benefits compared to ABS. First, PLA is easier to print because it has lower printing temperature which means that there is reduced risk of experiencing printer jams and it uses less energy. Also, PLA during printing produces less odor and fewer harmful emissions making it more suitable for use in indoor environments. Moreover, the degree of warping by PLA is significantly low than that of ABS hence more stable prints without the need for heated bed. Finally, unlike petroleum based ABS, PLA comes from renewable resources such as cornstarch.
Ease of Printing With PLA
PLA printing is particularly straight forward in comparison with other thermoplastics. Some sources such as All3DP, MatterHackers, and 3D Insider claim that PLA’s lower extrusion temperature reduces warping risks and eliminates the necessity for a heated bed. This makes it an ideal material for beginners. In addition to this aspect being biodegradable, absence of toxic fumes makes it safer for classroom or home printers compared to other materials like ABS. Its dependability together with predictability leads to consistent print quality thereby enabling reliable reproduction of even complex shapes or fine details repeatedly.
Environmental Impact of PLA
Polylactic Acid (PLA) is preferable because it has a lesser environmental impact when compared to other plastics like ABS. Made from sources such as maize starch or sugarcane, PLA uses less fossil fuel during its manufacture and produces fewer greenhouse gas emissions. Several studies have shown that the biodegradability of PLA in industrial composters is an added benefit to its eco-friendliness (3Dnatives; Filaments.ca; NatureWorks). However, one should remember that PLA biodegrades slowly under natural conditions, requiring specific ones for more efficient breakdown. However, despite these facts, it remains a better ecological alternative for 3-D printing.
Applications for PLA Filament
Due to its versatile properties, PLA filament is widely used across many industries. This material features among the most widely used feedstocks in the field of 3D Printing. Some people consider using PLA while making prototypes as this material is easy and safe to work with and guarantees good visual fidelity with small details required. Due to its safety and low environmental impact, this type of plastic is often used by teachers for creating models in their classes or supplying them with teaching aids meant for different subjects. Additionally, it has smooth finishes which are useful in producing fine details inside objects designed for use by consumers or artists who make decorative items out of them. Sustainability means that some goods may be created without spending too much time on production procedures which require delicate handling due to the quality of print obtained.
When to Use ABS Filament in 3D Printing
3D printing with ABS filament is a great option when strong, durable and heat resistant 3D prints are required. ABS is particularly suitable for functional prototypes, end-use parts, and products subject to mechanical stress according to sources such as Simplify3D, All3DP or 3Dnative. For example, it can be used in the automotive industry such as in making enclosures for electronic devices or even tools since its ability to withstand higher temperatures makes it ideal for these sectors. Also, post-processing techniques like sanding, acetone smoothing and drilling can be applied on ABS material thereby improving its finish and mechanical properties. Thus, if you need a 3D print that is hard-wearing against wear and tear as well as heat resistant then ABS filament is undoubtedly the most recommended.
Strength and Durability of ABS Parts
ABS parts are known for their incredible strength and durability which allow them to be used in harsh environments. ABS has high tensile strength and impact resistance qualities needed by parts under mechanical pressure. The filament can tolerate substantial abrasion hence appropriate for functional elements requiring long-term performance retention. Moreover, its inherent resistance towards high temperature makes sure that it remains stable through all heat-exposed situations. These features collectively establish ABS among the most fitting materials for producing solid resilient 3D-printed objects of various uses.
Heat Resistance and High Temperature Applications
ABS filament’s ability to withstand heat makes it an excellent material for use in high temperature applications. That at temperatures up to 100 degrees Celsius, ABS retains its shape. Thus, ABS can be used in vehicle parts that may get heated like these ones sometimes. It is also used in the manufacture of kitchenware where hot environments are a norm. In this case, the presence of heat resistant properties not only helps to prolong the life of items printed from ABS but also guarantees safety as well as reliability in different thermal-sensitive applications.
Post-Processing ABS Prints
In a nutshell, post-processing ABS prints can greatly enhance both aesthetic and functional qualities of the final product. There are different types of finishes that can be applied to ABS prints. Among them include sanding which aids in smoothening out rough patches on the surface and vapor smoothing using acetone which gives it a burnished glossy look. Painting is another common method employed afterwards so as to allow personalization and improve the outlook. Furthermore, installation procedures such as gluing or welding often take place where ABS components are concerned; this ensures strong joined surfaces with no ridges or gaps whatsoever. Hence these techniques do not just make ABS printed objects more attractive but also improve their toughness together with usability.
Comparing PLA and ABS to Other Filaments
When it comes to comparing PLA and ABS to other filaments, some of the factors that ought to be considered include strength, flexibility, ease of use and impact on the environment. PLA being a biodegradable thermoplastic from renewable resources such as maize starch is very easy to print with minimal warping and is suitable for fine detail work and low stress applications. However, PLA has less heat resistance and mechanical strength than ABS as well as other engineering grade materials. ABS, notorious for its strong mechanical properties and capability to sustain high heat levels is often used in the production of functional prototypes or end-use parts although it requires higher printing temperatures and proper ventilation due to fumes emission potential.
Filaments like PETG (Polyethylene Terephthalate Glycol), differ from PLA or ABS but still offer sufficient strength, are flexible enough while being easy to print thus they can be used in many different applications. Another option among alternatives is Nylon Filament which boasts superior tensile strength, durability & abrasion resistance even if hard to print because they are moisture sensitive & use higher processing temperatures. Furthermore, flexible filaments including TPU (Thermoplastic Polyurethane) provide an exceptional elasticity that gives them unbeatable flexibility useful when you want a rubber-like material.
Ultimately, the choice between PLA, ABS, and others depends on specific project requirements balancing factors like mechanical properties; user-friendliness; environmental performance; or finally what the part’s ultimate purpose will be after printing.
PLA vs PETG: Which to Choose?
The choice between PLA and PETG is a complex one. However, PLA is more suited for easy printing as it can be derived from renewable resources and biodegradable materials. Moreover, PLA offers a great surface finish and minimal warping, which makes it ideal for low-stress applications. Nevertheless, the heat resistance found in PETG and its durability are not present in PLA. In contrast to that, PETG has better balance of strength and flexibility than PLA, thus it is more useful for functional parts that will be exposed to considerable wear. In addition, compared with PLA, PETG is more resistant to temperature variations as well as UV exposure. Therefore if one considers ease of printing and environmental impact then PLA seems to be the right option while considering durability and mechanical performance; PETG works best.
Using PLA and ABS Filaments Together
Combining PLA with ABS filaments in one print is difficult due to their distinct printing requirements and properties. The key to success lies in effectively managing their unique characteristics:
- Adhesion and Temperature Control: Melting temperatures and adhesion of PLA differ from those of ABS. It is important that you use a 3D printer with dual extruder having independent temperature control on each filament. The extrusion temperature for PLA is lower (about 190-220°C), while that for ABS is higher (about 220-250°C).
- Bed Preparation: Proper bed adhesion is crucial. On a heated bed at about 50-60°C, PLA sticks well whereas an ABS needs a higher bed temperature of approximately 90-110°C. For both materials, consistent adhesion can be achieved by using a heated bed made of PEI (Polyetherimide) or similar surfaces.
- Combining Strengths: Printing certain portions of a model using PLA and others with ABS could maximize their respective strengths. Smoothness as well as better printability are the primary reasons why some sections need to be done in PLA; by contrast, other parts call for strength or resistance against heat hence logically requiring ABS. The combination’s effectiveness would depend on careful design as well as slicing techniques.
- Bonding: Combining PLA and ABS often requires additional bonding methods. At the junction between these two materials, specific adhesives used in 3D printing can hold them together.
Leveraging these factors through understanding and management will allow you benefit from unique advantages of PLA and ABS respectively when they are combined into one printed model.
Tips for Successful 3D Printing with PLA
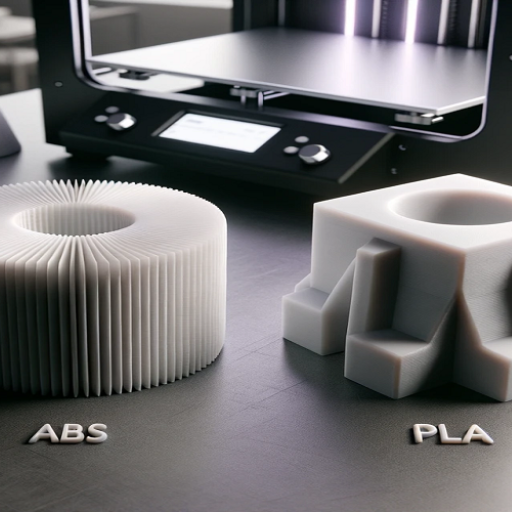
- Optimum Temperature Levels: Confirm that the extruder is set between 190-220°C as specified by the manufacturer of your filament for smooth and even printing.
- Appropriate Bed Adhesion: Use a heated bed at approximately 50-60 °C to stick PLA better. It also helps when you add a thin layer of glue stick or painter’s tape since this will enhance its adhesiveness and inhibit warping.
- Avoid Overheating: Provide good ventilation around your printer to prevent heat from accumulating excessively; otherwise, it may make PLA too soft and ruin your print quality.
- Maintain Print Speed: Set your printer speed at 40-60 mm/s so as to ensure consistent printing. Higher speeds may lead to weak layer bonding and other print imperfections.
- Filament Storage: PLA is hygroscopic, meaning it absorbs moisture from the air. Therefore, always keep it in a dry and cool place with some desiccant packets to safeguard its printing quality.
- Routine Maintenance: Keep cleaning your nozzle and bed regularly so that no residue is left behind which might cause you print problems. als, it is possible to l
You can improve your experience with 3D printing using PLA if you follow these tips consistently, thus eventually producing high-quality prints.
Optimal Print Temperatures for PLA
The optimal printing temperature of PLA is generally from 190 to 220°C; though, this can differ slightly with regard to the brand and type of PLA filament your are using.
- MatterHackers suggests that people should print it between 190°C and 220°C depending on the characteristics of the specific filaments.
- All3DP states that you can begin at around 200°C, then adjust accordingly for printer and filament brands since higher quality filaments may have varying slight setting requirements.
- Prusa Knowledge Base advises starting at lower than 210°C but for better results set extruder temperature between 210-220°C, adjusting as needed.
Therefore, there is an optimal starting point at approximately 200oC, while one can fine-tune within the range of between 190 and 220oC to suit different situations for this purpose.
Avoiding Print Failures When Using PLA
The best three online sources will help you come up with important ideas for avoiding PLA print failures. Begin with making sure the bed sticks by using blue tape, glue stick or heated bed. Keep mattress clean so as to reduce printing problems from build-up of residue. The other way is through careful calibration of printer settings that incorporates adjusting print speed, layer height and extrusion multiplier for more precise prints. Lastly, management of filament quality is done through proper storage in a dry environment containing desiccant packs and inspecting it for signs of moisture or brittleness. It is important to observe these practices in order to minimize print failures and create consistent outcomes when using PLA.
Finishing and Post-Processing PLA Prints
Besides improving surface quality and functionality, one can do further finishing and post-processing of PLA prints.
- To obtain better results and to smooth out layer lines it is advised to use different grit sizes of sandpaper starting with a coarse one that is around 200-400 grits up to very fine one as high as 2000 grits. Wet sanding aids in achieving a higher level finish.
- However, before sanding, MatterHackers suggests filling minor gaps and blemishes with filler primer. It creates smooth surface for painting or other additional techniques applied during finishing.
- PLA printouts can be sealed by spraying them with either polyurethane or acrylic clear spray so as to improve their durability without losing the natural beauty of the material. Alternatively, the polish done on sealed prints using polishing compounds yields shiny finishes.
It therefore follows that, if you want your PLA prints to look more professional; you will have to sand them first then prime and finally seal them.
Cost Considerations for PLA and ABS Filaments
Prices of PLA and ABS filaments depend on some factors. Usually, the price of PLA is lower, starting from about $20 to $30 per kilogram. This fact attracts low budget beginners. However, ABS filament is somewhat higher in cost at about $25-35 per kilo. Its comparative highness emanates from its better durability and heat resistance which make it necessary for many specific uses. Moreover, both kinds of filaments may have fluctuating prices as a result of different brands, quality or even additional features like increased strength or availability of color.
Price Comparison of PLA and ABS Filaments
That PLA is cheaper than ABS in terms of costs incurred. In general, based on 3D Insider data, most standard grade PLA retails for approximately $15-30/kg making it an economical choice for applications requiring fused deposition modeling (FDM). The figures are also close when All3DP published that high-quality PLA ranged anywhere between 20$ and 35$, contingent on the maker while some extra benefits were realized such as toughness increase or color choice.
The average price range for ABS filament varies from about $20-$40 per kilogram. The costlier price is usually supported by the more lasting material nature and ability to withstand heat by this polymer; this becomes very essential for other demanding functionalities. Nevertheless, depending on brand attributes such as size/weight/shape etc., retailers might offer varying price points. For instance if compared generally with ABS it can be seen that despite their affordability among majority users these materials’ prices differ particularly for springy thermoplastics like polylactic acid than acrylonitrile butadiene styrene (ABS), as indicated before.
Long-Term Durability and Cost Efficiency
When thinking about their long-term durability and cost-effectiveness, it is important to take into account the overall lifespan and performance of PLA and ABS filaments. Overall, PLA has been found to have a lower durability than ABS due to its tendency to degrade under sunlight or extreme temperatures as stated by All3DP. However, in terms of being environmentally friendly and ease of handling, it is an ideal choice for short term projects.
ABS has better long-term durability due to higher thermal stability and greater resistance against impacts. ABS also tends to warp while printing making it more difficult to print with compared with other filaments like PLA which emit fumes as well. When printing functional parts that require continuous use, however, ABS might be preferred over the rest.
That initial cost of investing on ABS may be high in comparison with PLA but the former’s superior mechanical properties make this kind of investment one worth the effort especially when considering the industrial applications. On the other hand, PLA could be more cost effective if used for short term purposes or when they are used for decorative purposes because it is cheaper at first instance and requires less complicated printing.
In summary, while PLA is affordable for numerous different uses, ABS lasts longer term enabling it be used where there is significant exposure to harm thus becoming a cheaper option.
Frequently Asked Questions (FAQs)
Q: What are the main differences between PLA and ABS in 3D printing?
A: PLA (Polylactic Acid) and ABS (Acrylonitrile Butadiene Styrene) are both popular 3D printer filaments, but they have different properties. PLA is made from renewable resources like corn starch and is biodegradable, while ABS is made from petroleum and is not biodegradable. PLA has a lower printing temperature and is known for being easy to print with, while ABS requires higher temperatures and is known for its strength and durability.
Q: Is PLA or ABS better for beginners in 3D printing?
A: For beginners, PLA is generally better than ABS. This is because PLA has a lower printing temperature, emits less harmful fumes, and adheres well to the print bed without the need for a heated bed. These characteristics of PLA make it easier and safer to use for those new to the 3D printing process.
Q: How does the glass transition temperature of PLA compare to ABS?
A: The glass transition temperature of PLA is typically around 60-65°C, while ABS has a higher glass transition temperature around 105°C. This means that PLA parts are more likely to soften and deform at lower temperatures compared to ABS.
Q: What are the strength differences between PLA and ABS?
A: ABS is much stronger and more durable than PLA, which makes it suitable for applications requiring toughness and impact resistance. However, PLA is also quite strong but not as tough as ABS. For lightweight and low-stress applications, PLA is usually adequate and preferred due to its ease of use.
Q: Are there any safety concerns with using ABS compared to PLA?
A: When it comes to 3D printing, ABS requires higher temperatures, which can release more fumes compared to PLA. ABS also typically requires good ventilation during printing due to potentially harmful emissions. PLA emits fewer fumes and is considered safer for home and desktop 3D printing environments.
Q: Can both PLA and ABS be used with most desktop 3D printers?
A: Yes, both PLA and ABS can be used with most desktop 3D printers. However, due to its lower printing temperature requirements and easier handling, PLA is more commonly used in a wider range of desktop 3D printers. ABS might require a printer with a heated bed and an enclosed build area to achieve optimal results.
Q: What are the environmental impacts of using PLA vs ABS?
A: PLA is made from renewable resources and is biodegradable, making it more environmentally friendly compared to ABS, which is made from petroleum and is not biodegradable. PLA also generates fewer emissions during the printing process, reducing its environmental footprint.
Q: How do the printing requirements of PLA differ from ABS?
A: PLA has lower printing requirements compared to ABS. PLA filament prints at lower temperatures around 180-220°C and does not necessarily require a heated bed. ABS prints at higher temperatures of 220-250°C, often requiring a heated bed at around 90-110°C and sometimes an enclosed build area to prevent warping and ensure better print quality.
Q: What applications are ABS and PLA each best suited for?
A: PLA is ideal for applications where ease of printing, biodegradability, and a good surface finish are important. It is often used for prototypes, educational purposes, and decorative objects. ABS, on the other hand, is better suited for applications requiring higher strength, durability, and resistance to higher temperatures, such as mechanical parts, automotive components, and consumer electronics housings.
Q: Have any new materials been developed that combine the properties of both PLA and ABS?
A: Yes, new materials like PETG filaments have been developed, which combine some properties of both PLA and ABS. PETG is stronger than PLA and more flexible, like ABS, while being easier to print with and less prone to warping. This makes PETG a popular choice for users looking for a balance between the characteristics of PLA and ABS.