Due to its balanced strength, ductility, and hardness properties, medium carbon steel is a versatile material used across different industries. This type of steel typically comprises about 0.3% – 0.6% carbon, making it suitable for structural applications without sacrificing machinability or welding ease. In this blog post, we will look at some of the unique qualities of medium carbon steels, their various types, and how they are applied in everyday life and industries. By the end of this article, readers will have an in-depth understanding of the role medium carbon steel plays in engineering and manufacturing fields and its benefits and drawbacks in various uses.
What is Medium Carbon Steel?
Image source: https://www.tsmsteel.com/
Medium Carbon steel contains, on average, between 0.3% and 0.6% carbon by weight. Its composition balances the two dichotomous factors—ductility and strength—making it suitable for varied applications in diverse environments. Medium carbon steel can be heat treated to increase hardness and wear resistance, resulting in better performance under harsh operating conditions. The combination of toughness and machinability is frequently employed when designing components such as gears, axles, or structural supports, requiring both toughness and machinability at once.
What is the carbon content in medium carbon steel?
Generally, the carbon content of medium carbon steel falls between 0.3% and 0.6%. This is the exact concentration that allows medium carbon steel to have a combination of strength, ductility, and hardness. Literature sources, including material science articles and industry handbooks, confirm that this range has been preferred for applications demanding higher performance and toughness alongside machinability criteria. The capability of making medium-carbon steels harder through heat treatment makes them suitable for use in more demanding applications.
How does medium-carbon steel differ from low and high-carbon steel?
Medium-carbon steel differs from low and high-carbon steel primarily in their respective carbon content levels, which translates into different properties. Low-carbon steels containing less than 0.3% C possess excellent ductility and malleability. Thus, they are more easily shaped or welded but cannot be hardened like medium carbons. Conversely, high-carbon steels contain more than 0.6% C, which imparts increased strength and hardness but renders them relatively brittle with a lower degree of ductility, making them challenging to work with in some applications. Thus, medium-carbon steels emerge as an intermediate option, striking a balance between these two extremes, allowing them to be used for various engineering and manufacturing purposes where resistance against breaking and machining properties are vital.
What are the common uses of medium carbon steel?
Because of the balance between its properties, medium carbon steel is used in various industries. Gear manufacturing, axle manufacturing, and shafting have been widely used due to their high strength and toughness. Automotive components, structural components, and machinery parts are other typical applications. Moreover, it is suitable for making tools and dies because it can be heat-treated, improving its durability and wear resistance. This makes medium carbon steel ideal for more demanding applications in both industrial and construction situations.
What are the Properties of Medium Carbon Steel?
There are several vital reasons why medium carbon steel is appropriate for numerous uses. It typically contains 0.3 to 0.6% carbon, providing adequate strength, hardness, and ductility. The toughness of this type of steel is excellent; by hardening through heating, its mechanical properties improve, hence an increment in hardness as well as wear resistance on the material after hardening takes place. Also, its machinability weldability enables complex shapes or components to be made easily using Medium Carbon Steel. Finally, it can resist deformation under load, thus becoming a dependable material for high-stress environments that may demand such attributes from a metal product. In sum, these characteristics blend together so that whenever high performance/durability matters most, medium carbon steel becomes handy here.
What mechanical properties define medium carbon steel?
Medium steel carbon has several mechanical properties, making it very effective for different uses. These are some of them:
- Yield Strength: Generally speaking, medium carbon steels have yield strengths that range around 260 to 600 MPa, depending on their specific compositions and heat treatments. This implies that the material can be deformed under load without permanent changes.
- Tensile Strength: Tensile strength lies between 410 and 800Mpa in most medium carbon steels. It measures the maximum stress a material can withstand when stretched before breaking, meaning high-stress applications can confidently employ this metal.
- Hardness: Medium carbon steel can have hardness values ranging from approximately 150 to 300 HB (Brinell Hardness). Heat treatment techniques such as quenching and tempering can achieve higher levels of hardness, thus improving wear resistance.
- Ductility: Being able to be stretched into different shapes without fracturing is an attribute that characterizes this type of steel. With elongation percentages typical for this class being about 10% – 20%, the process becomes suitable for forming purposes.
- Impact Resistance: Medium carbon steels generally have good impact strength, which ensures integrality during sudden stresses because their life cycles sometimes involve dynamic loads or shock loading.
These mechanical properties make medium steel carbon versatile. It combines durability, strength, and resistance to wear, making it applicable in many other areas.
How does tensile strength vary in medium carbon steel?
The tensile strength of medium carbon steel varies based on several factors, including the specific carbon content, alloying elements, and applied heat treatment. These types often contain between 0.3% and 0.6% C, so such a range directly affects their tensile strength. It should also be noted that quenching and tempering upon heating drastically strengthen the steel’s tensile strength, increasing its maximum values between 410 and 800 Mpa. The availability of additional alloying elements like manganese or silicon can further modify their tensile properties, thus enhancing their performance in different areas.
What is the wear resistance of medium carbon steel?
The wear resistance of medium carbon steel is commendable, and it can be used in applications that involve friction and wear. Information gathered from various reputable sources indicates that its wear resistance mainly depends on the amount of carbon it contains and the heat treatment it undergoes. A higher carbon content typically results in increased hardness, which is associated with improved wear resistance; by refining the microstructure of the steel, heat treatments such as quenching and tempering help to further enhance these properties. Thus, medium carbon steel is often employed in manufacturing tools, gears, and other parts that require wear resistance at a balance between durability and performance.
What are the Types of Medium Carbon Steel?
Medium carbon steel comes in different grades according to its composition and intended use. Some of the main types are:
- C1045 Steel: This type has a carbon content of approximately 0.45%, which makes it useful for high-strength applications such as shafts or gear materials.
- C1050 Steel: With about 0.50% carbon, C1050 is preferred for making wear-resistant components and tools while maintaining its hardness and ductility.
- C1060 Steel: This type contains around 0.60% carbon; hence, it has a greater hardness than other types of cutting tools and blades
These distinct kinds have individual traits suited to varied industrial needs, enabling their versatile application across engineering and manufacturing industries.
What are the different grades of medium carbon steel?
Specific carbon percentages and alloying elements identify the various grades that medium carbon steel is often divided into. These include common grades such as:
- AISI 1040: With about 0.40% carbon, this grade has good weldability and moderate strength, making it suitable for axles and crankshafts.
- AISI 1050: The carbon content of AISI 1050 is approximately 0.50%, thus exhibiting high tensile strength, which is required in gears or tool manufacturing that demand more wear resistance.
- AISI 1060: AISI 1060 contains about 0.60% carbon and is well known for its excellent hardness and strength; hence, it is used in the production of many high-performance tools and blades.
These grades reflect the diversity of the application areas and properties of medium carbon steels meant to address different engineering requirements.
How are types of medium carbon steel categorized?
Medium carbon steel types are classified by their carbon content, ranging from around 0.25% to 1%. Furthermore, I learned through my research that they have subcategories based on uses, such as structural applications, automotive parts, and tooling. This means that there are further classifications under each one such as industrial structures like building materials including beams and channels etc., automotive components like engine parts (pistons), body frames, and tools with varying degrees according to whether they’re used for cutting or finishing processes among others; all these being other categories within this same basic type classification system used in recognition by industry professionals who might not need finer distinctions until quite recently when attempts began at formulating standardized nomenclature primarily through ISO certification programs designed mainly around them rather than just relying upon variations between manufacturers themselves; then again some firms still adhere strictly either because they lack financial resources needed develop all possible options while others believe this approach lends itself best only those instances where specific products must meet certain regulatory standards established either nationally or globally.
What role does manganese play in medium carbon steel?
Manganese plays a critical role in medium carbon steel, improving its overall features. As a deoxidizer, it primarily functions to eliminate undesired elements that interfere with the production process of steel. It results in improved strength and hardness. The metal also becomes more brutal and resists wear; hence, it can be used for demanding applications where a resilient material is needed. This improves the toughness and ductility, making energy absorption possible without breakage. Manganese presence generally extends the versatility of medium-carbon steels in many uses, including those in automobiles and construction materials.
How Does Medium Carbon Steel Compare to Other Steel Types?
Medium carbon steel occupies a balanced position in the hierarchy, combining strength with ductility. Compared to low-carbon steels, which have less than 0.25% C levels, medium-carbon steel has more strength and hardness due to higher carbon content . However it is less malleable than lower versions which are softer and more ductile. On the other hand, when matched against high carbon steels (>0.60C), medium carbon steels possess inferior hardness and wear resistance but show improved toughness, hence becoming less brittle. This combination makes it very useful for someone who needs both solid and tough materials like car parts or machinery in general.
What are the critical differences between medium-carbon and high-carbon steel?
On average, medium carbon steel has 0.25% to 0.60% carbon content, while high carbon steel has over 0.60% carbon. The difference in their carbon contents influences these mechanical properties of the metals. A sheet made of plug weld is solid and ductile because it contains about 0/3% to 0/5% Carbon, making it ideal for automotive parts where impact resistance is required. In contrast, hard high-carbon steels are also brittle; thus, they can be used in making manufacturing tools and other applications requiring high strength. Moreover, medium or mild steel can be welded more easily than high-carbon steel, which often necessitates special techniques for preventing cracking during welding. The type of material selected will depend on the desired balance between hardness, toughness, and manufacturability.
What are the characteristics of low-carbon steel compared to medium carbon steel?
Low-carbon steel typically contains up to 0.25% carbon, which renders it much softer, more ductile, and more malleable than medium-carbon steel. Low-carbon steels are inferior to mediums in terms of ultimate tensile strength but superior in elongation at break, especially when subjected to bending formabilities during manufacture. This means materials such as low-carbon steel are easier to work with within the context of fabrication processes, where joining operations like welding and machining them into valuable shapes may need to be done.
However, some wear resistance and hardness may be lost along the way; hence, this might not be suitable for high-tensile components compared to intermediate types like medium-carbon ones. Overall, I would opt for low-carbon steel if my aim was getting a material that can allow easy shaping or joining, while for sections needing greater strength and durability, I would choose medium-carbon steel like machinability and cost factoring, such as casting arising from ease of fabrication. Consequently, low-carbon steel is best used when it requires shaping and joining. In contrast, medium carbon steel is preferable for parts that need more strength and durability.
Why is mild steel considered different from medium carbon steel?
In contrast to medium-carbon steel, mild steel is also called low-carbon steel because of its lower carbon content, usually 0.05% – 0.25%. This lower percentage of carbon makes this material softer, more malleable, and easier to weld and shape than its counterpart, which has between 0.26% and 0.60% of carbon. Nonetheless, mild steel may be easily shaped into various forms while remaining cost-effective; it lacks the hardness and strength inherent in medium carbon steel, making it ideal for parts subject to wear and high loads. Additionally, mild steel is versatile and commonly used in construction activities and manufacturing, whereas medium carbon steel is more specialized in mechanical qualities.
What are the Grades of Medium Carbon Steel?
On the other hand, medium carbon steels are defined by their differing elements, including the range of their C (carbon) contents, which range from 0.26% to 0.60%. Some commonly used ones include:
- A36: Structural Steel widely used in construction that is easily welded or machined
- 1010: Generally used for general purposes, it offers moderate strength and good ductility.
- 1045: For instance, gears and axles require increased strength and higher hardness; this grade would be appropriate.
- 1050: It contains a relatively high amount of carbon, so its use could improve surface resistance to wear.
These grades exhibit different mechanical properties, making them suitable for various industrial applications where toughness and strength count.
How are medium carbon steel grades determined?
They are classified into medium carbon steel grades based on their carbon content and resultant mechanical properties. The method involves a composition analysis that is carried out to ascertain the percentage of carbon and alloying elements such as manganese, silicon, or chromium. Moreover, mechanical tests that include tensile, yield, and hardness measurements aid in evaluating the materials’ behavior under different circumstances. Manufacturers often follow standards set by entities such as SAE (Society of Automotive Engineers) or ASTM International that stipulate performance requirements for various grades to guarantee uniformity and reliability when used across sectors.
What are the typical applications for different grades of medium carbon steel?
In my research, I have encountered different kinds of medium carbon steel grades with specific uses based on their qualities. For instance, people widely use A36 steel in engineering works because it can be quickly joined through welding and has high-strength properties, especially in building construction. 1010 steel, with good malleability features, can be used in making non-strength demanding parts like car parts and general machinery tools. 1045 steel is often employed in manufacturing gears with higher strength than other gears due to its more excellent toughness, while axles require adamant ones. These unique aspects of each grade make them well-suited for particular roles within different industries, from construction to motorcar engineering.
How do the properties of medium carbon steel grades affect their use?
Medium carbon steel grades are characterized by properties that significantly impact applications in different sectors. This higher carbon content is attributed to these grades’ increased tensile strength and hardness, making them suitable for parts subjected to wear and heavy loads. For example, 1045 steel is used in heavy-duty applications like gears and axles due to its high strength and longevity. On the other hand, steels with lower carbon content, such as 1010, provide better ductility and weldability; hence, they are fit for manufacturing automotive parts that involve forming or shaping processes. Furthermore, alloying elements within these grades may affect characteristics like corrosion resistance and heat treatment response, thus enabling manufacturers to select particular grades based on performance demands and environmental concerns. Therefore, proper selection ensures that products meet industry standards for reliability and safety, which consequently enhances operational efficiency in construction and automotive engineering.
What Applications Benefit from Medium Carbon Steel?
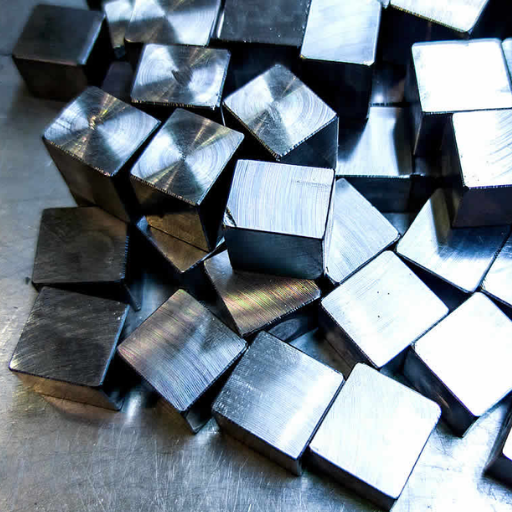
Medium carbon steel is versatile because it combines strength, ductility, and wear resistance in one material. Typical areas for use include crankshafts, gear systems, or suspension components found in automotive manufacturing, where durability is essential. In the construction industry, medium carbon steel is usually applied as structural beams or reinforcements that cope with stress. It also has a place in machinery production, where machine ability and toughness are vital assets, such as shafts and brackets, which provide services to locomotives, such as rail cars. Consequently, this feature, alongside cost effectiveness, makes medium-carbon steel widely applicable across various industries requiring good quality but relatively cheap materials.
In what industries is medium carbon steel commonly used?
A variety of industries use medium carbon steel because of its favorable characteristics. The automotive sector applies it to manufacturing vital elements such as gears, axles, and frames that require high strength and wear resistance. Also, the construction industry benefits from using medium carbon steel for structural purposes like beams, columns, and reinforcing bars that support buildings and bridges. Additionally, machine parts, tool making, and heavy equipment manufacturing benefit from the machinability and durability of medium carbon steels. Medium carbon steel is, hence, a material used in many areas due to its versatility.
What are the advantages of using medium carbon steel in manufacturing?
There are many plus sides to using medium carbon steel in manufacturing. It is one of the most durable materials under different conditions because of its perfect combination of strength and toughness achieved by a balanced composition. I also like its ability to carry heavy loads and resistance to wear, which is crucial for machine parts that constantly undergo stress. In addition, it can be easily machined, thus supporting precision manufacturing processes that enable the formation of intricate shapes and designs. Lastly, it has an advantage over highly alloyed steels in terms of cost, making me able to have high performance without a considerable increase in production costs, which is ideal for producers and consumers.
How does the carbon content affect the performance of medium carbon steel in applications?
The amount of carbon present in the metallic alloys called medium-carbon steels typically varies between 0.3% -0.6%, which significantly impacts their properties when used for various applications. On the one hand, a higher carbon content makes these materials harder and have higher tensile strengths, enabling them to resist more stress and, hence, becoming suitable for making solid gears or axles, among others. However, higher amounts of carbon make them less ductile, reducing their toughness so that they may be brittle under certain conditions. Thus, there should be a careful balance between the two levels so that these medium-carbon steels can maintain sufficient toughness. At the same time, they achieve the desired strength to make them versatile for industries requiring both durability and formability, unlike those that do not.
Frequently Asked Questions (FAQs)
Q: What is medium-carbon steel?
A: Medium-carbon steel is a type of carbon steel with a carbon content ranging from 0.30% to 0.60%. It balances strength and ductility, making it suitable for various industrial applications.
Q: What are the properties of medium-carbon steel?
A: Medium-carbon steel’s properties include moderate tensile strength, good wear resistance, and balanced ductility. It also has a higher manganese content, which improves hardenability and strength.
Q: How does medium-carbon steel differ from high-carbon steel?
A: Medium-carbon steel has a lower carbon content than high-carbon steel, which typically contains more than 0.60% carbon. Due to the higher carbon content, high-carbon steel is more rigid but less ductile compared to medium-carbon steel.
Q: What are the types of medium-carbon steel?
A: The types of medium-carbon steel can be classified based on their specific carbon content and alloying elements. They include plain medium-carbon steel and alloy medium-carbon steel, which may contain additional elements like chromium, nickel, or molybdenum for enhanced properties.
Q: What are the standard grades of medium-carbon steel?
A: Common grades of medium-carbon steel include AISI 1040, AISI 1045, and AISI 1050, as defined by the American Iron and Steel Institute (AISI). These grades vary in their specific carbon and manganese content.
Q: Where is medium-carbon steel commonly used?
A: Medium-carbon steel is commonly used in applications requiring a balance of strength and ductility. Typical uses include automotive components, machinery parts, axles, gears, and structural steel.
Q: How is medium-carbon steel processed?
A: Medium-carbon steel is often processed through heat treatment methods such as quenching and tempering. The steel is heated to a high temperature in these processes and then rapidly cooled to improve hardness and strength.
Q: What are the differences between low-carbon steel and medium-carbon steel?
A: Low-carbon or mild steel has a carbon content of less than 0.30%. It is more ductile and accessible to weld than medium-carbon steel, which has a higher carbon content and offers greater strength and wear resistance.
Q: How do the properties of medium-carbon steel and high-carbon steel compare?
A: Medium-carbon steel has moderate tensile strength and ductility, while high-carbon steel is more complicated and brittle due to its higher carbon content. High-carbon steel is better for applications requiring high hardness, such as cutting tools and blades.
Q: What are the standard grades of high-carbon steel?
A: Common grades of high-carbon steel include AISI 1060, AISI 1070, and AISI 1095. These grades are characterized by their high carbon content, which enhances hardness and wear resistance but reduces ductility.