What is Gear Cutting and Why Is It Important?
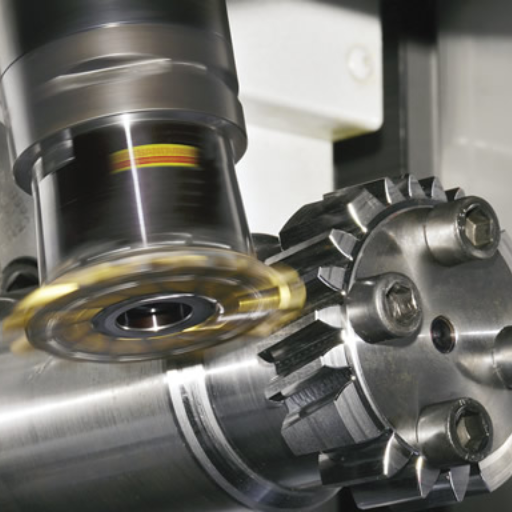
Image source: https://www.ctemag.com/
Understanding Gear Types: Spur, Helical, and More
When we talk about gear types, it is important that we know the three main classes which include helical gears, spur gears and bevel gears among others.
Spur Gears: The most commonly used type of gears are spur gears. They have straight sets of teeth on them and they are placed on parallel shafts. They are known for their simplicity and efficiency hence ideal for high-speed motion applications that need a direct transfer.
Helical Gears: Helical gears have teeth that are sliced into faces at an angle. This results in a helix shape making it operate smoothly and quietly than the spur gear. They can be applied to non-parallel and perpendicular shafts thus allowing more flexibility in design but requiring complex methods of production.
Bevel Gears: Bevel gears contain teeth shaped conically enabling them to transmit force between intersecting axles. These types of gears are typically employed in differential drives which may change direction of a rotating axis. Varieties such as straight bevel gears to spiral bevel gears possess varying performance characteristics with a smooth and silent running spiral bevel gear being one of them.
Applications and Key Moments in Gear Cutting
Gear cutting has been important in many industrial applications and serves sectors such as automobiles, aerospace or even the everyday home appliances. Each application requires specific gears to ensure smooth running and efficiency. Such as, in the car industry, gears are essential for transmissions that allow power from the engine to be transferred to the wheels. Notably, these gears are crucial for control systems in aviation and landing gear mechanisms since they should be reliable and have great accuracy.
Eli Whitney’s invention of a milling machine in early 19th century was one such defining moment in gear cutting history. This discovery fundamentally changed manufacturing by allowing mass production but retaining consistency when creating gears. The subsequent significant milestone was achieved through computer numerical control (CNC) equipment development. By this technology came an era of precision engineering which enabled producing intricate gear geometries with minimum human input. Moreover, recent developments in 3D printing and additive manufacturing have opened up new possibilities for gear design by expanding the limits of possibility for traditional designs into more complex, customized shapes.
The Role of Gear Cutting in Modern Machinery
How to Choose the Right Milling Machine for Gear Cutting?
Comparing Horizontal and Vertical Milling Machines
The differences between the horizontal and vertical milling machines can be best understood by looking at their unique qualities and uses. Horizontal milling machines have a spindle that is horizontally oriented, allowing cutters to take material off the side of the workpiece . This makes them suitable for cutting heavy materials at high speeds as well as offering improved stability on thicker components subjected to long cuts. They are useful in gear cutting, slotting and working on many sides of a part concurrently.
On the other hand, vertical milling machines have their spindles oriented vertically, making them ideal for tasks where highly detailed or precision work is required. These devices offer good visibility of the cut area hence they are useful when intricate gear designs or complex geometries need to be made. In addition to being easy to set up and operate, operators like vertical mills because they are often used in die sinking, mould making and other applications demanding high precision and surface finish.
Horizontal milling machines will shine in heavy duty applications and mass production while vertical ones are loved for their accuracy, versatility and ease of use in smaller, detailed activities. Choosing between these options depends on the needs specific to your project such as size, complexity as well as how many pieces you plan on making per order when it comes to gear manufacturing.
Key Features to Look for in a Gear Cutting Machine
I. It is important to consider some key factors while selecting a gear cutting machine that will guarantee efficiency, accuracy and versatility.
- Accuracy and Precision: The device should be highly accurate and precise in order to produce the desired gear dimensions and tolerances. Examples include automated control systems and precision guides.
- Versatility: Look for a gear cutting machine that can handle different gear types, sizes, or materials. Such machines can have adjustable parameters and interchangeable tools.
- Durability and Build Quality: Choose machines made of sturdy materials for durability during heavy use. For longer life and dependable operation, use quality build components such as stiff framework, durable bearings.
- Ease of Use: Machines with easy-to-use interfaces, clear controls, etc., improve overall productivity. This may involve features like digital displays or compatibility with CNC.
- Cutting Speed and Efficiency: High-speed cutting allows for fast production times on these machines. To do this correctly is to use efficient motor systems in the appropriate direction of cut.
- Maintenance and Support: Consider purchasing machinery that requires little maintenance but has strong customer service support options. Also look out for parts availability among other aspects such as comprehensive service manuals.
Essential Milling Machine Attachments and Accessories
To make milling machines more functional and productive, they can be fitted with an assortment of attachments and accessories. Following are the most fundamental:
- Vises: It is quite important that you have a high-quality vise to hold the workpiece safely when milling. Accuracy in precision vises makes sure there is stability and accuracy with reduced deflection and vibration.
- Rotary Tables: Multi-axis machining and angular cutting operations cannot be done without rotary tables. They allow complicated geometries as well as patterns by allowing precise rotation of the workpiece around a vertical axis.
- Collets and Collet Chucks: Small diameter work pieces and cutting tools need collets to grip them securely. The collet chucks offer a range of collet sizes for various applications thus making it a versatile gripping mechanism.
- End Mill Holders: These are used to attach end mills together with other cutting tools. They must ensure minimal run out and proper alignment so as to achieve accurate cuts.
- Digital Readouts (DROs): This improves accuracy by providing actual position feedback helping manual operation. It shows exact coordinates to increase precision during machining hence reducing errors.
- Boring Heads: Boring heads are employed for high-precision hole enlargement purposes. They come with adjustable bore diameters as well as specific aligning holes, which is necessary for tight-tolerance application needs.
- Clamp Sets: Clamps or clamping kits hold the workpiece in different orientations, supporting more complex setups. It’s necessary to prevent movement of the piece while at work, safety should also be ensured.
Preparing for Gear Cutting: Essential Steps and Setup
1. Selecting the Right Equipment
The process of choosing a suitable gear cutting machine as well as the cutting tools cannot be underemphasized. For instance, among several other devices that are available such as hobbing machines, shaping machines, grinding machines and more. A good selection should be based on the size of the gear, its material and desired level of precision.
2. Material Selection
To have enough strength and wear resistance as per what is required, it is significant to use appropriate materials for the gear blank. It can be made out of steel, copper or aluminum alloys. The material choice depends on factors like load conditions that will exist in the gearbox.
3. Precision Setup and Alignment
To have an accurate working condition, the machine has to be correctly set up and aligned with respect to this workpiece-in-question. This includes using proper fixtures to secure a gear blank in place and ensuring that the position of cutter is accurately calibrated. Use precise measuring instruments and adjustment modes for efficient results.
4. Calculating Gear Parameters
In order to achieve flawless gears production accurate calculations must be performed regarding parameters like number of teeth, module or pressure angle. These parameters determine how the gears will function hence their appropriate values should reflect on how they will serve their intended purposes.
5. Lubrication and Cooling
Adequate lubrication and cooling are necessary during cutting operations so as to prevent overheating and tool wear. Appropriate coolant selection and its correct application may improve surface finish while prolonging tool life.
6. Monitoring and Quality Control
Monitoring the cut process continuously coupled with stringent quality control measures helps in maintaining operational effectiveness at every stage involved hereof; hence keeping up with inspection processes on dimensions-thus determining their final profile alongside surface finishing-that must comply with certain allowances being within specified limits throughout all these stages is essential.
Step-by-Step Guide to Cutting a Spur Gear
- Material Selection
- Choose a gear blank that is made from the appropriate material for your intended use. Some of these materials include steel, aluminium and brass.
- Gear Blank Preparation
- Make sure that the gear blank is machined to accurate dimensions such as diameter and thickness. Fix it firmly on the worktable and align it properly.
- Setup Your Gear Cutting Machine
- Set up your machine with a hob or milling cutter that can cut spur gears without any problem.
- Aligning and calibrating the cutting tool so that it is in its correct position towards the gear blank.
- Calculating Gear Parameters
- Find out the main metrics of gearsign – number of teeth, module, pressure angle etc. These things will determine if you want your machine to function effectively as well as which other machines they are compatible with.
- Lubrication and Cooling Setup
- For avoiding overheating of cutting tools and reducing wear on them, apply proper lubricant and coolant. This helps to keep up good quality surface roughness on the part with a final cut worn.
- Cutting the Gear Teeth
- It involves setting feed rate and speed according to material type and specific tool parameters before commencing into gear cutting process.
- The final tooth is gradually brought out by repetitively going deeper until desired profile is reached in incremental steps.
- Monitoring and Quality Control
- Adjustments are also required during cutting operation to continuously monitor this process. The reason for checking dimensional accuracy, surface finish, tooth profile regularly; all this have been mentioned above hereunder at “Monitoring & Quality Control” step-wise subdivision as stated above in (a) Monitoring & Quality Control).
- Carry out periodic quality control checks while cutting so that both tolerance limits as well as specifications may be maintained throughout this procedure when making gears.
Advanced Gear Cutting Techniques and Tips
Optimizing Cutting Tool Selection
Advanced gear cutting makes it crucial for you to pick the right cutting tool. Some of these tools include TiN (Titanium Nitride) or TiAlN (Titanium Aluminum Nitride), which have an incredible effect on improving both the lifetime and performance of tools. This reduces friction as well as wear, leading to higher rates of cutting while at the same time ensuring that they can be used for longer periods.
Custom Tool Geometry
Efficiency and accuracy can also be increased by employing custom tool geometry specifically developed to suit different material types and gear designs. Changing the shape of a tool in order to match your specific gears dimensions and specifications could assist in achieving good surface finish and correct tooth profiles.
High-Speed Machining
While maintaining quality, high-speed machining methods can significantly reduce the time spent in production. However, this demands accurate management of feed rates, spindle speeds and depth of cut. Advanced CNC machines with real-time monitoring functions and adaptive control systems can enable smooth performance during high-speed operations.
Dry Machining Practices
Dry machining techniques that use minimum quantity lubrication or advanced air cooling methods may offer advantages especially for environmentally conscious manufacturing situations. Through this approach, savings are made on coolant disposal costs while at the same time reducing potential risks related to thermal damage both on gears and machine parts.
Continuous Improvement and Monitoring
Through implementing continuous improvement strategy via such monitoring technologies like vibration analysis as well as inline metrology, any divergence from perfect cutting conditions is immediately detected thus rectified. This ensures consistent quality between various batches of gears.
How to Maintain and Troubleshoot Your Milling Machine?
For one to properly use a milling machine, it is important to ensure that it is well maintained. Clean the machine regularly in order to prevent swarf and debris from gathering on it and affecting its accuracy and wearing its parts. Lubricate all moving parts as recommended by the manufacturer to reduce friction and prevent rusting. Check alignment and calibrate the machine when necessary for accurate functioning. For instance, examine worn cutting tools and replace them.
While troubleshooting, consider identifying any strange sounds or vibrations that may indicate mechanical problems. When the machine fails to start, first verify electrical connections as well as fuses. On the other hand, if there are any abnormal operational behaviors of the machines you could try checking whether there are software errors or outdated firmware’s in it Monitoring devices are useful in detecting problems at an early stage thus reducing downtime due to damaged equipment. When carrying out maintenance or trying to fix a problem always consult with the user’s manual and follow appropriate safety measures.
Regular Maintenance Tips for Optimal Performance
- Scheduled Inspections: Schedule inspections that are regular in order to detect and address wear and tear before they become big problems. For example, the inspection might involve checking alignment, inspecting belts and gears, or even ascertaining whether all components are in good condition.
- Lubrication: Regularly apply lubrication to moving parts and components based on guidance from the manufacturer. Proper lubrication reduces friction, prevents overheating and increases machine life span.
- Cleaning: Ensure removal of swarf, dust and debris after every use to keep the milling machine clean. A clean machine tends to operate more effectively and is less likely to get damaged or experience wear.
- Calibration: At certain intervals calibrate the machine so it can maintain precision. This involves checking tool alignment as well as adjusting them, workholding alignment among others like machine settings.
- Replacing Worn Parts: Examine vital elements such as cutting tools on a regular basis including belts and bearings. In case there are any worn parts observed one should replace them so as to have best performance levels thus avoiding unexpected breakdowns.
- Monitoring System Health: Use diagnostic tools for tracking machines health status. Detecting minor issues early through vibration analysis, temperature monitoring, performance tracking saves expensive repairs and downtime.
- Software Updates: Keep software of your machinery up-to-date for efficient operation of the miller. Periodic updates improve performance and fix bugs that enhance overall functionality.
Troubleshooting Common Gear Cutting Problems
In gear cutting, many aspects can arise which can have an impact on the quality and efficiency of gears. Listed below are some common problems encountered in gear cutting:
- Inaccurate Gear Dimensions: This may be as a result of wrong tools set-up or worn out cutting tools when the produced gears get inaccurate measurements. Always ensure that the tools are well calibrated and replaced if they start to show signs of weariness. Periodically check and maintain your tool setup to assure dimensional accuracy.
- Surface Finish Issues: This can arise from incorrect cutting parameters, blunt tools or lack of enough lubrication during manufacturing process resulting in poor surface finish of the teeth in gears. Follow optimum levels recommended by tool manufacturers for cutting speeds, feeds and depths. Replace or sharpen dull tools while ensuring proper lubrication during cutting process.
- Tooth Profile Errors: Inaccurate tooth profiles occur when there is improper formation of gear teeth perhaps due to misalignment or wear on the tool used. Make sure that the alignment between workpiece and cutter is perfect. Utilize highly accurate measuring devices to examine and keep correct position along with replacing worn-out tooling regularly.
When to Seek Professional Help: Key Indications
To preserve the efficiency and durability of your gear cutting operations, it is important to know when to seek professional help. Hence, here are few symptoms that shows that you are in need of a specialist:
- Persistent Quality Issues: In case you face challenges like wrong dimensions, tooth profile errors or surface finish problems that do not disappear despite taking corrective action, it may be time to consider consulting an expert. The issues persisting over time usually imply underlying difficulties which cannot be sorted without some specialized skills.
- Unusual Noises or Vibrations: If there exist any unusual noise or excessive vibration reported during the cutting process; they may indicate mechanical problem. This could come from misalignments or whatever tool set-up and component failure demanding for professional help in assessment and fixing.
- Frequent Downtime: Where repeated failures and troubleshooting attempts have resulted into frequent downtimes, hiring professionals can assist in identification of root causes thereby reducing downtime while increasing productivity.
- Complex Repairs or Upgrades: While doing intricate repairs or planning significant upgrades aimed at boosting operational efficiency associated with gears cutting, you will require professional knowledge so that things can be done correctly as well as safely. Experts can deliver advanced solutions to enhance your gear cutting processes using best practice methodologies.
Reference sources
- Practical Machinist Forum: Gear Cutting On a Horizontal Mill
- This forum thread discusses various experiences and techniques for cutting gears on a horizontal mill, including specific details about different diametral pitches (DP).
- Read more here
- The Home Machinist! Forum: Gears and Gear-Cutting on your Mill
- This discussion covers both vertical and horizontal milling machines, including references to useful resources like the Van Keurens Catalog and Handbook for threading and gear cutting.
- Read more here
- Hobby-Machinist Forum: Gears and Gear Cutting on the Milling Machine
- This thread offers detailed instructions and experiences from hobbyists on how to cut gears using both manual and milling machines, including photo-essays and complete tear-down manuals for precise gear tooth counts.
- Read more here
Frequently Asked Questions (FAQs)
Q: What are the basic steps involved in gear cutting on a horizontal milling machine?
A: The process of gear cutting on a horizontal milling machine involves several steps: setting up the milling machine, mounting the gear blank on an arbor, using a dividing head to index the gear teeth, choosing the appropriate gear cutter, and cutting the gear teeth via the milling process.
Q: What equipment is necessary for cutting gears on a horizontal milling machine?
A: The essential equipment includes a horizontal milling machine, dividing head, gear cutter, arbor, tailstock, and appropriate cutting tools. Depending on the specific requirements, additional tools like broaches or lathe may also be needed.
Q: How does a dividing head assist in the gear-cutting process?
A: A dividing head is crucial in the gear-cutting process as it enables the precise indexing of the gear blank. This ensures that each gear tooth is accurately positioned, allowing for the consistent and accurate creation of gear teeth.
Q: What are the differences between cutting spur gears and helical gears on a horizontal milling machine?
A: Cutting spur gears involves simple indexing and cutting straight teeth using the gear cutter. In contrast, helical gears require angular indexing to cut the teeth at an angle. This process involves more complex setup and machining processes compared to spur gears.
Q: Can hobby machinists effectively use horizontal milling machines for gear cutting?
A: Yes, hobby machinists can use horizontal milling machines for gear cutting; however, it requires a solid understanding of the machine setup, gear milling techniques, and indexing processes. It’s advisable to start with simpler projects and progressively tackle more complex gear systems.
Q: Why is the material of the gear blank important in the gear-cutting process?
A: The material of the gear blank significantly affects the gear-cutting process. Different materials have varying degrees of machinability and wear resistance, which can impact cutting speeds, tool wear, and the overall quality of the cut gear. It’s essential to choose the material based on the gear’s application and requirements.
Q: What is the role of a gear cutter in gear milling?
A: A gear cutter is a specialized cutting tool used to shape the teeth of gears during the gear milling process. The gear cutter’s profile must match the involute profile of the gear’s teeth to ensure precise and accurate tooth geometry.
Q: How is simple indexing different from compound indexing in gear cutting?
A: Simple indexing involves dividing the gear blank into equal parts using a dividing head, which is straightforward for cutting standard gears. Compound indexing, however, is used for non-standard gears and involves more complex calculations and setup to achieve precise tooth placement.
Q: What safety precautions should be taken while cutting gears on a horizontal milling machine?
A: Safety precautions include wearing appropriate protective gear like goggles and gloves, ensuring the milling machine and all components are securely fastened, keeping hands clear of the cutting area, and following proper operating procedures for the gear cutter and dividing head. Additionally, regular maintenance and inspection of the machine and tools are crucial to ensure safe operation.
Q: How does gear cutting on a horizontal milling machine compare to using other machines like a lathe?
A: Gear cutting on a horizontal milling machine is often preferred for its precision and versatility in producing various gear types. In contrast, using a lathe for gear cutting typically involves more manual operations and less specialized gear-cutting attachments, making the process more suitable for simpler or more customized gears. Each method has its advantages, and the choice depends on the specific gear requirements and available equipment.