What is Flame Cutting and How Does it Work?
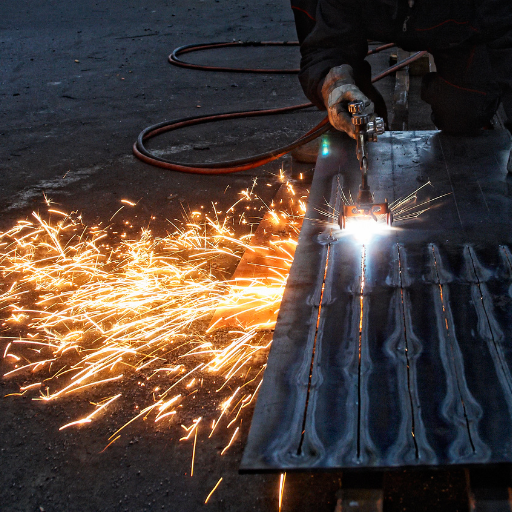
Understanding the Flame Cutting Process
Flame Cutting vs Other Methods
Flame cutting is different from other processes, like plasma cutting and laser cutting, in some ways. The technique of flame cutting, also called oxy-fuel cutting, is best for working with heavy steel plates that are often in some cases several inches thick because it cuts efficiently and cheaply. This makes it suitable for heavy-duty applications such as building ships and buildings.
On the other hand, plasma uses a gaseous medium to conduct electrical energy from the power source through the nozzle to the workpiece. On thin materials like this it can cut faster with cleaner edges than flame; yet on various metals it is versatile.
Laser technology on its part utilizes concentrated light beams that deliver precision and finesse leading to an improved finish making them perfect for delicate patterns as well as thin metal sheets unlike flame cuttings they tend to be costly especially when dealing with thicker material.
In conclusion, whereas flame cutting ranks first in terms of economical way of cutting very thick steel while plasma and laser cuttings beat it in terms of speed, precision and versatility of materials which suit different manufacturing needs.
Choosing the Right Fuel Gas for Flame Cutting
To cut flame, you need to select the right fuel gas which will bring about maximum performance and safety. Some fuel gases are commonly used in this process such as acetylene, propane and natural gas; each having its own set of characteristics:
- Acetylene: It is known for its high flame temperature around 5720°F (3160°C), which makes the cut fast and precise, making it ideal for applications that require a lot of heat energy and quick preheating. When it comes to cutting thick steel, it works well but it costs more than other fuel gases.
- Propane: Propane has got a lower burning temperature of approximately 4579°F (2526°C) compared to acetylene but with excellent combustion efficiency thus leading to low operating costs. This is good for use in general purpose such as cutting, heating or brazing operations. Its burn is cleaner and easy to handle though it takes long time for preheating.
- Natural Gas: Natural gas on the other hand has still lower flames temperatures at around 3720°F (2049°C). However, natural gas is the least expensive option that is often used for cutting and heating purposes in huge industrial areas like factories. This requires special equipment but saves significant amount of money and includes prolonged hours usage.
What Materials Can Be Cut Using Flame Cutting?
Best Practices for Cutting Carbon Steel and Mild Steel
When cutting carbon steel and mild steel, it is important to follow the best practices for optimal results and efficiency. Below are some of the key guidelines extracted from top resources:
- Preheat the Material: Before cutting, let steel undergo preheating process to minimize chances of thermal shock and improve quality of cut especially for thicker parts. The most desirable preheat temperature is around 300-600°F (150-315°C).
- Proper Torch Setup: Ensure that the cutting torch has been set up according to the nozzle size and gas pressures recommended. A suitable cutting tip should be used that matches the thickness of the steel being cut. Maintain a constant distance as well as angle between the torch and material for clean cut.
- Adjust Flame Settings: Adjust flames properly so as to achieve neutral or slightly carburizing one. Such an equilibrium allows efficient cutting without excessive slag formation. A neutral flame will have a sharp inner cone surrounded by well-defined outer envelope.
- Maintain Cutting Speed: Maintaining consistent speed during this operation is very important; too slow risks overheating, excessive slag while too fast may result in incomplete cuts. Change speeds depending on thickness of material and quality of cuts desired.
- Use of Guides and Rulers: Using straight edges or steel guides assists in keeping straight precise cuts particularly on long lines. This guarantees accuracy and minimizes wastage.
- Regular Maintenance: You must keep your equipment in good working condition all times possible while undertaking such practice such as flame cutting mild steels with carbon content in them. Cleaning must be done frequently; also check if there are any blockages on torch tips plus wearings made on it, lastly make sure gas lines together with their fittings do not leak at all.
Limitations of Flame Cutting for Aluminum and Stainless Steel
On the other hand, even though flame cutting is effective for carbon and mild steel it has major constraints when used on stainless steel and aluminum. One of the key issues is that aluminum and stainless steel have a higher melting point than carbon steel. As such the oxy fuel process involving exothermic reaction with iron turns out to be ineffective and sometimes impossible for these metals.
Flame cutting is thus obstructed by rapid heat dispersion because aluminium is highly conductive leading to irregular cut edges and excess material loss. It also contains no iron in its composition which provides necessary conditions for quick oxidization during oxy-fuel cutting.
Consequently, cutting stainless steel becomes more difficult due to chromium content that forms an oxide film which resists oxidation. This leads to poor quality cuts as well as possible surface contamination of the metal resulting in lower corrosion resistance.
Consequently, alternative methods like plasma or laser are preferable when it comes to aluminum or stainless steel because they can make cleaner, more accurate cuts without limitations inherent in flame-cutting.
Plasma Cutting: How Does It Compare to Flame Cutting?
Basics of the Plasma Cutting Process
Starting plasma cutting involves making an electrical path of ionized fuel or rather a plasma through the torch and then in the work. In this plasma, electrical arc is produced by power supply. This plasma is sufficiently hot so as to melt metals while high velocity gases blow away molten metal creating a cut. Majority of these cutters employ compressed air or nitrogen which makes them come in handy and effective.
According to the first results on Google search, the process can be broken down into several steps:
- Arc Initiation: The electric arc ionizes gas thus forming a plasma.
- Plasma Generation: The electric arc ionizes gas thus forming a plasma.
- Cutting Action: The temperature at this point can rise as high as 30,000°C (54,000°F), melting the metal.
- Material Removal: A jet of ionized gas with very high speed blows the molten material aside thus leaving a clean cutting surface.
Advantages and Disadvantages of Plasma Cutting
Advantages:
- Precision and Accuracy: Modern plasma cutters, often integrated with CNC systems, are highly precise and accurate resulting in ability to make complex shapes with great detail.
- Speed: Plasma cutting is much faster than traditional methods especially on thin materials.
- Versatility: CCan pass through many types of metals like iron sheets, stainless steel, aluminium, brass or copper with simplicity.
- Minimal Heat Affected Zone: The high speed and focused heat of the plasma stream cause a small heat-affected zone which minimizes warping and thus ensures neater edges.
- Efficiency: Plasma cutting is efficient as it takes little time to set up thereby leading to increased productivity in industries.
Disadvantages:
- Operating Costs: After being considered as economical at first instance, plasma cutters can have expensive long-term running cost due to consumables and power consumption involved.
- Noise and Fumes: TBecause the process produces considerable noise and fumes; thus it requires proper ventilation system as well as operators’ protective clothing.
- Limited Thickness: When using oxy-fuel cutting method on very thick items compared to other techniques; thus this makes plasma cutting less effective when used on them.
- Quality on Certain Materials: Due to their thermal conductivity features, various kinds of metal like aluminum and copper may not produce good outcomes in terms of properties that are metal characteristics by means of plasma cutting technology
- Initial Equipment Cost: This can be an obstacle for small companies since acquiring a high quality system for plasma cutting might require a large sum of money.
When to Choose Plasma Cutting vs Flame Cutting
Plasma cutting or flame cutting – this is the question that depends on several factors such as material type, thickness, precision requirement and cost implications:
- Material Type: Flame cutting works well with ferrous metals like iron and steel while plasma cutting is skilled at non-ferrous ones like aluminium and stainless steel.
- Material Thickness: For hard materials that are above 1 inch (25mm), flame cutting is more effective in delivering higher energy. Plasma cutting takes care of thin materials typically below 1 inch.
- Precision Requirements: Plasma cuttings are more precise and deliver cleaner cuts, especially for thin materials. This makes it a better option for intricate designs; on the other hand, flame cutting may produce more slag and require some extra finishing work though it is very strong.
- Speed and Efficiency: In high volume applications where productivity is still an important factor to consider plasma cutting wins hands down as it has minimal setup time hence saves a lot of time when working with thinner materials. On the other hand, slow flame cutting gives excellent results on thicker sections.
- Operational Costs: Plasma cutters are more expensive to purchase initially including higher operating costs due to consumables such as electricity while producing faster speeds. Compared to plasma cutters which have consumables including electricity thus being expensive to operate, flame cutters are relatively cheap for thick steels since they use oxygen together with fuel gas.
What Are the Key Differences Between Flame Cutting and Plasma Cutting?
Comparing Cutting Speed and Efficiency
Cutting speed and efficiency comparisons between flame cutting and plasma cutting are influenced by a number of factors. By way of the leading Google resources, plasma cutting is generally faster and more efficient, specifically on thinner materials. In fact, thin metal sheets can be cut at 500 inches per minute by plasma systems, which significantly saves production time. Moreover, plasma cutting has very low preheat time requirements thus tending to increase its efficiency.
On the other hand, flame cutting means slowly moving with a lot of costs in case one wants to cut thick metallic sections. Although it is much slower than other methods it is cost-effective when it comes to severing heavy ferrous metals because operational expenses are lower. Flame cutting also involves a preheating stage that results into large amounts of slag thus needs further finishing processes.
Summarily: As concerns speed in thin materials and different metal kinds, plasma cutting provides the best choice for customers while flame cutting option still remains robust as well as economical for thicker steel sections.
Examining Cutting Quality and Tolerances
When it comes to assessing the quality of cuts made by cutting machines and their tolerance levels, plasma and flame cutters have their own pros and cons. With respect to Google’s top sources, it has been established that plasma cutting is generally superior on thinner materials for cutting quality, which has smoother edges and less dross. Narrower kerf widths resulting from the use of plasma systems are achieved through high precision that is required in highly detailed works having very tight tolerances. This implies that there will be fewer material wastes as well as lesser need for any post-production touch-ups.
On contrary, flame cutting performs better on thicker steel sections but usually leaves rougher edges and more slag when compared with plasma cutting. Since the broader kerf would sometimes give less accurate cuts with wider tolerances thus making this process unsuitable for detailed work. However, when dealing with heavy steel thicknesses, as opposed to the cost factor alone, flame cutting is still a reliable approach.
To sum up, while plasma cutting best suits thin materials requiring high precision clean cuts; flame cutting benefits in thicker sections where cut speed and edge smoothness have a lesser significance.
Cost Considerations: Flame Cutting vs Plasma Cutting
On the contrary, plasma cutting has higher initial equipment costs as well as more costly consumables. The operating expenses can escalate mainly for frequent consumable replacements. However, for thin materials, this method cuts at faster speeds and it also improves efficiency thus potentially drawing back some of the cost disadvantages through enhanced productivity and reduced processing time later on.
To sum up, even though plasma cutting may be more expensive than flame cutting due to precision and efficiency in thinner material economics and is typically preferred while working with thicker steel sections.
How to Choose the Right Cutting Services for Your Project?
Factors to Consider for Oxy Fuel Cutting Services
When considering oxy fuel cutting services for your project, it is essential to evaluate several key factors in order to get the best results:
- Material Thickness: Oxy- fuel cutting is well suited for thicker steel plates usually above one inch. For thinner materials, other cutting methods may be more appropriate.
- Edge Quality: If you are demanding a good edge finish, bear in mind that oxy-fuel cutting can cause dross and might need additional post-processing to clean the edges.
- Cutting Speed: In thin material works this method is slower than others such as plasma cutting. However, it excels at quickly shearing through thick sections.
- Budget: The cost-effectiveness of oxy fuel cutting is due to lower equipment and operational expenses. It uses cheap readily available gases like oxygen, acetylene or propane.
- Portability: This attribute makes it suitable for on-site jobs and repairs; hence an added advantage over heavier non-movable cutting systems.
Evaluating Cutting Work for Different Projects
When concerning the requirements and limitations, it is important to determine the appropriate cutting operation in different projects. The most popular websites advise focusing on these crucial aspects for an educated decision:
- Precision and Tolerance: Varied cutting methods provide differing levels of accuracy. Laser cutting, for instance, is highly precise and therefore suitable for detailed models while oxy fuel cutting may work better on objects that are less detailed and thicker.
- Material Compatibility: Different processes are compatible with specific materials. Some examples include plasma cutting which utilizes stainless steel and aluminum as well as waterjet cutting that can be applied in case you want to cut other substances such as plastics composites or stone.
- Project Scale and Volume: For large-scale production batches, CNC cutter setups offer repetitive automated activities. On the contrary, smaller one-off projects would require manual procedures or simpler tools which might be cheaper alternatives too.
Understanding the Capabilities of Cutting Machines
Selecting the right tool for your project calls for an understanding of various cutting machines’ capabilities. Only top websites and current notes can provide a summary analysis which is as follows.
- Laser Cutting: It is best suited for complex designs needing high accuracy, that’s why it is perfect for metal, plastic with some woods and it gives nice tidy cuts.
- Plasma Cutting: It may not have much detail as laser cutting but it works best on ferrous metals such as stainless steel, steel and aluminum. Plasma cutting is very fast and efficient; it can be used for medium to heavy materials.
- Waterjet Cutting: This technique employs high-pressure water stream mixed with abrasive elements to cut different hard substances like glass, metal or even composite. Thereby, this method does not produce heat hence non-thermal distortion leads to precise cuts.
Reference sources
- Summary: This source from ESAB provides a comprehensive overview of the flame cutting process, explaining how it works and its application in separating and shaping steel components. It discusses the use of oxygen and a fuel source to create the necessary flame for melting materials, making it a valuable resource for understanding the fundamentals of flame cutting.
- Summary: MicroStep’s information on flame cutting, also known as oxyfuel cutting, delves into one of the oldest cutting processes in metal processing. It highlights the utilization of a fuel-oxygen mixture to cut metal, making it suitable for readers seeking detailed insights into the technical aspects of flame cutting.
- Summary: BICO Steel’s flame cutting services are showcased in this source, emphasizing the ability to accurately produce complex shapes from steel plates and blocks up to 32 inches thick. The inclusion of CNC precision burns and other related services makes this source helpful for those looking for practical applications and services related to flame cutting in the industry.
Frequently Asked Questions (FAQs)
Q: What is the difference between flame cutting and plasma cutting?
A: Flame cutting, also known as oxyfuel cutting, is a thermal cutting technique that uses a flame cutter with fuel gas and oxygen to cut through thick materials. Plasma cutting, on the other hand, uses an ionized gas (plasma) at high temperatures to melt and blast away the material to be cut. Flame cutting is often preferred for its simplicity and cost-effectiveness, while plasma cutting is more versatile and can cut through a wider range of materials and thicknesses.
Q: How does flame cutting work?
A: Flame cutting is a process that involves a flame cutter, which uses a mixture of fuel gas and oxygen to create a high-temperature flame. This flame heats the material to be cut to its ignition temperature, and a jet of oxygen is then directed at the heated area to combust and blow away the metal, thus cutting through it. This technique is primarily used for cutting thick steel materials.
Q: What materials can plasma cutting be used on?
A: Plasma cutting can be used to cut a variety of materials, including steel, stainless steel, aluminum, brass, and copper. Its ability to cut through both thick and thin materials makes it a versatile cutting method, suitable for a wide range of industrial applications.
Q: What are the advantages of flame cutting machines?
A: Flame cutting machines are beneficial for their simplicity, cost-effectiveness, and ability to cut through very thick steel plates, often up to several inches thick. They are ideal for heavy-duty industrial applications where precise but robust cuts are needed. Flame cutting technology is also well-suited for bevel cutting and other specialized cutting operations.
Q: When is flame cutting preferable over plasma cutting?
A: Flame cutting is preferable when cutting very thick steel materials due to its high cutting capacity and lower cost compared to plasma cutting devices. It is also advantageous in situations where simplicity and low operating costs are essential, such as in heavy industrial environments.
Q: What are some limitations of flame cutting?
A: Flame cutting can be limited by its relatively slower cutting speeds and lower precision compared to plasma or laser cutting. It is also less versatile, as it is primarily used to cut steel and some other ferrous metals. Additionally, the process can introduce more heat-affected zones, which might require additional finishing steps.
Q: How does laser cutting compare to flame cutting?
A: Laser cutting, like plasma cutting, offers higher precision and versatility compared to flame cutting. It uses a focused laser beam to achieve fine cuts, making it ideal for intricate shapes and thinner materials. While laser cutting can be more expensive than flame cutters, its precision and efficiency make it a preferred method for high-quality and detailed cutting needs.
Q: What safety precautions should be taken during flame cutting?
A: Safety precautions for flame cutting include wearing protective gear such as gloves, goggles, and flame-resistant clothing. Proper ventilation is necessary to avoid inhaling harmful fumes. It’s also important to handle the cutting tool carefully and ensure that the area to be cut is free of flammable materials. Regular maintenance of flame cutting devices is essential to ensure safe and efficient operation.
Q: Can plasma and flame cutting be automated?
A: Yes, both plasma and flame cutting can be automated using CNC (computer numerical control) systems. This allows for precise and repeatable cutting operations, increasing efficiency and reducing human error. Automated flame cutting machines are common in large-scale industrial settings where high cutting throughput is required.
Q: What factors should be considered when choosing between flame cutting and plasma cutting?
A: Important factors to consider include the thickness and type of material to be cut, required precision and cutting speed, budget, and the specific needs of the cutting operation. Flame cutting is generally chosen for its cost-effectiveness and ability to cut through very thick materials, while plasma cutting is selected for its versatility, speed, and precision.